Puolikiinteän metallin valuprosessin historia ja suuntaus
Vuodesta 1971 lähtien Yhdysvaltojen Massachusetts Institute of Technologyn DBSpencer ja MCFlemings ovat keksineet uuden sekoitusvalumenetelmän (sekoitusvaletun), eli Srr15%pb reologisen lietteen valmistuksen pyörivällä kaksoistynnyrisellä mekaanisella sekoitusmenetelmällä, puolikiinteä metalli (SSM) Valimotekniikka on kokenut yli 20 vuoden tutkimusta ja kehitystä.
Seoksella valmistettuja seoksia kutsutaan yleensä ei-dendriittisiksi seoksiksi tai osittain jähmettyneiksi valuseoksiksi (osittain kiinteät valuseokset). Koska tätä tekniikkaa käyttävillä tuotteilla on korkealaatuisia, korkean suorituskyvyn ja erittäin seostettuja ominaisuuksia, niillä on vahva elinvoima.
Sotilastarvikkeiden käytön lisäksi se alkoi keskittyä esimerkiksi automaattisten ajoneuvojen avainkomponentteihin, esimerkiksi autojen pyöriin, jotka voivat parantaa suorituskykyä, vähentää painoa ja vähentää romun määrää. Siitä lähtien sitä on vähitellen sovellettu muille aloille, ja se on tuottanut korkean suorituskyvyn ja lähes verkon muotoisia osia. Myös puolikiinteän metallin valuteknologian muovauskoneita on otettu käyttöön yksi toisensa jälkeen.
Tällä hetkellä on kehitetty ja valmistettu puolikiinteä valuvalu 600-2000 tonnista, ja muodostettujen osien paino voi olla yli 7 kg. Tällä hetkellä tätä prosessitekniikkaa käytetään laajalti Yhdysvalloissa ja Euroopassa. Puolikiinteän metallin valuprosessia pidetään yhtenä lupaavimmista lähes verkonmuovaus- ja uusista materiaalivalmistustekniikoista 21. vuosisadalla.
Prosessin periaate
Tavallisessa valuprosessissa ensisijaiset kiteet kasvavat dendriittien muodossa. Kun kiinteän faasin suhde saavuttaa noin 0.2, dendriitit muodostavat jatkuvan verkkorungon ja menettävät makroskooppisen juoksevuutensa. Jos nestemäistä metallia sekoitetaan voimakkaasti jäähdytysprosessin aikana nestefaasista kiinteään faasiin, tavallisen valun aikana helposti muodostuva dendriittiverkko luu rikkoutuu, jotta dispergoitu rakeinen rakenne säilyy ja se suspendoidaan jäljellä olevaan nestefaasiin. Tällä rakeisella ei-dendriittisellä mikrorakenteella on edelleen tietty reologia, kun kiinteän faasin suhde saavuttaa 0.5-0.6, joten tavanomaisia muovausprosesseja, kuten painevalu, suulakepuristus, muottien taonta jne., Voidaan käyttää metallin muodostamiseen.
Metalliseoksen valmistus
On olemassa monia menetelmiä puolikiinteiden seosten valmistamiseksi. Mekaanisten sekoitusmenetelmien lisäksi viime vuosina on kehitetty sähkömagneettisia sekoitusmenetelmiä, sähkömagneettisia pulssikuormitusmenetelmiä, ultraäänivärähtelyä sekoittavia menetelmiä, seosnesteen pakotettua virtausta kaarevia kanavia pitkin ulkoisen voiman alaisena ja jännityksen aiheuttamaa sulamisaktivaatiota. Menetelmä (SIMA), ruiskutusmenetelmä (Ospray), kontrolliseoksen kaatolämpötilan menetelmä jne. Niistä sähkömagneettinen sekoitusmenetelmä, seoksen kaatolämpötilan säätömenetelmä ja SIMA -menetelmä ovat lupaavimpia menetelmiä teollisiin sovelluksiin.
1. Mekaaninen sekoitusmenetelmä
Mekaaninen sekoitus on varhaisin menetelmä puolikiinteiden seosten valmistamiseksi. Flemings et ai. valmisti onnistuneesti tina-lyijylejeeringistä puolikiinteän lietteen käyttämällä sekoituslaitteistosarjaa, joka koostui samankeskisestä hammastetusta sisä- ja ulkosylinteristä (ulompi sylinteri pyörii ja sisempi sylinteri oli paikallaan); H. Lehuy et ai. käytti sekoituslapaa alumiinin valmistukseen-puolikiinteä liete kupariseoksesta, sinkki-alumiiniseoksesta ja alumiini-piiseoksesta. Myöhemmät sukupolvet paransivat sekoitinta ja valmistivat puolikiinteän ZA-22-seoksen lietteen käyttämällä kierukkasekoitinta. Parannuksen avulla lietteen sekoitusvaikutus paranee, sulan metallin kokonaisvirtauslujuus muotissa vahvistuu ja sula metalli tuottaa alaspäin kohdistuvaa painetta, mikä edistää kaatamista ja parantaa harkon mekaanisia ominaisuuksia.
2. Sähkömagneettinen sekoitusmenetelmä
Sähkömagneettinen sekoittaminen on pyörivän sähkömagneettisen kentän käyttö indusoidun virran tuottamiseksi sulaan metalliin. Sula metalli liikkuu Lorenin magneettisen voiman vaikutuksesta saavuttaakseen tarkoituksen sekoittaa sulaa metallia. Tällä hetkellä pyörivän magneettikentän luomiseksi on pääasiassa kaksi menetelmää: toinen on perinteinen tapa siirtää vaihtovirtaa induktiokelassa; Toinen on pyörivä kestomagneettimenetelmä, jonka esitteli Ranskan C.Vives vuonna 1993 ja jonka etuna on sähkömagneettinen induktio. Laite koostuu korkean suorituskyvyn kestomagneettimateriaaleista, joilla on suuri magneettikentän voimakkuus. Muuttamalla kestomagneettien järjestelyä sula metalli voi tuottaa ilmeisen kolmiulotteisen virtauksen, mikä parantaa sekoitusvaikutusta ja vähentää kaasun tarttumista sekoituksen aikana.
3. Jännityksen aiheuttama sulamisen aktivointimenetelmä (SIMA)
Jännityksen aiheuttama sulamisaktivaatiomenetelmä (SIMA) on muodonmuutoksen esimuodostamista perinteisille harkoille, kuten suulakepuristukselle, valssaukselle ja muulle lämpökäsittelylle puolivalmiiksi tankoiksi. Tällä hetkellä mikrorakenteella on voimakkaasti pitkänomainen epämuodostunut rakenne, ja sitten se kuumennetaan. ei-dendriittisen rakenteen harkon saamiseksi.
SIMA -prosessin vaikutus riippuu pääasiassa alemman lämpötilan kuumakäsittelyn ja sulattamisen kahdesta vaiheesta tai kylmän työvaiheen lisäämisestä näiden kahden välille, prosessia on helpompi hallita. SIMA-tekniikka soveltuu useille seoksille, joilla on korkea ja matala sulamispiste, ja sillä on ainutlaatuisia etuja ei-dendriittisten seosten valmistuksessa, joilla on korkeammat sulamispisteet. Sitä on sovellettu menestyksekkäästi ruostumattomasta teräksestä, työkaluteräksestä, kupariseoksesta ja alumiiniseoksesta, ja se on saanut ei-dendriittisen rakenteen seoksen, jonka raekoko on noin 20 um. Siitä on tulossa kilpailukykyinen menetelmä puolikiinteiden raaka-aineiden valmistamiseksi. Sen suurin haitta on kuitenkin se, että valmistetun aihion koko on pieni.
4. Viime vuosina kehitettyjä uusia menetelmiä
Viime vuosina Southeast University ja Japanin Arety Research Institute ovat havainneet, että kontrolloimalla seoksen valulämpötilaa primaarinen dendriittirakenne voidaan muuttaa pallomaiseksi rakenteeksi. Tämän menetelmän ominaisuus on se, että ei tarvitse lisätä seosaineita eikä sekoittaa. V. Dobatkin et ai. ehdotti menetelmää jauhimen lisäämiseksi nestemäiseen metalliin ja ultraäänikäsittelyn suorittamiseksi puolikiinteän harkon saamiseksi, jota kutsutaan ultraäänikäsittelyksi.
Muovausmenetelmä
Puolikiinteille seoksille on monia muovausmenetelmiä, lähinnä:
1. Uudelleenmuovaus (Rheocast) sekoittaa sulan metallin voimakkaasti nesteestä kiinteäksi jäähdytysprosessin aikana ja suoraan hydraulisesti heittää tai pursottaa saadun puolikiinteän metallilietteen tietyllä kiinteällä fraktiolla.
Esimerkiksi R. Shibata et ai. lähetti kerran puolikiinteän metalliseoksen lietteen, joka oli valmistettu sähkömagneettisella sekoitusmenetelmällä, suoraan painevalukoneen ruiskutuskammioon muodostamista varten. Tällä menetelmällä valmistettujen alumiiniseosvalujen mekaaniset ominaisuudet ovat korkeammat kuin suulakepuristusvalujen, ja ne vastaavat puolikiinteitä tiksotrooppisia valuja. Ongelmana on, että puolikiinteän metallilietteen varastointi ja kuljetus on vaikeaa, joten käytännön sovelluksia ei ole paljon.
2. Tiksokastaminen (Thixoforming, Thixocast)
Valmistettu ei-dendriittinen rakenneharko lämmitetään uudelleen kiinteän ja nesteen kaksivaiheiseen vyöhykkeeseen sopivan viskositeetin saavuttamiseksi ja sitten painevalu tai suulakepuristus.
EOPCO, HPM Corp., Prince Machine, THT -puristimet Yhdysvalloissa, Buhler Sveitsissä, IDRA USA, Amerikan Italpresse Italiassa, Tuottaja USA Kanadassa, Toshib a Machine Corp. Erikoislaitteet kiinteän alumiiniseoksen tioformointiin. Tämä menetelmä on helppo automatisoida aihion lämmitys ja kuljetus, joten se on nykyään puolikiinteän valun päämenetelmä.
3. Ruiskupuristus
Sula metalli jäähdytetään suoraan sopivaan lämpötilaan puolikiinteän lietteen sijasta käsittelyn jälkeen ja ruiskutetaan onteloon muodostamaan tietyissä prosessiolosuhteissa. Esimerkiksi Thixoforming Development Center Wisconsinissa Yhdysvalloissa käytti tätä menetelmää magnesiumseosten puolikiinteään valamiseen. Professori KK Wang Cornellin yliopistosta Yhdysvalloissa ja muut ovat kehittäneet samanlaisen magnesiumseosruiskuvalulaitteen. Puolikiinteä liete lisätään materiaaliputkesta ja ruiskutetaan onteloon asianmukaisen jäähdytyksen jälkeen.
4. Matalan lämpötilan jatkuva valu
Niin kutsuttu matalan lämpötilan jatkuva valu on valumenetelmä, jossa sulan metallin tulistusta säädetään noin 0 ° C: een ja pakkojäähdytys suoritetaan muotin alla, kuten kuviossa 4 esitetään. jatkuva valu ja rikkoutuminen voi tapahtua valssilangan jatkuvan valssauksen aikana. Siksi prosessilla on suuri merkitys.
5. Nauhan jatkuva valu
Flemings käytti Sn-15%pb alhaisen sulamispisteen metallia suorittamaan nauhavalukokeita ja analysoi lämmönsiirtoa, jähmettymistä ja muodonmuutosta. Nauhan paksuuden uskotaan liittyvän telan paineeseen, kiinteän faasin suhteeseen, reologiseen leikkausnopeuteen ja jatkuvaan valunopeuteen. Kun erityinen paine suulakepuristuksessa on suuri, mikroerotusta edistetään. Pinnan ja sisäisen laadun ja mittatarkkuuden varmistamiseksi on välttämätöntä valvoa tiukasti puolikiinteän metallin valmistuksen prosessiparametreja, kuten kiinteän faasin suhdetta, ensisijaisen kiteen muotoa ja poistetun metallin määrää.
Korkean sulamispisteen omaavien metallien, kuten fosforipronssisen Cu-Sn-P-seoksen (Cu-8%Sn-0.1%P), nesteen lämpötila on 10300 ℃, jota on vaikea lämpökäsitellä. Sillä on ilmeinen vaikutus tästä puolikiinteästä seoksesta valmistettuun ohutlevyyn. Tällä hetkellä on mahdollista valmistaa puolikiinteitä ruostumattomasta teräksestä valmistettuja harkoja ja nopeita työkaluteräsharkkoja, joilla on erinomainen organisointi.
Tekniset edut
Puolikiinteän painevaluprosessin edut voidaan tiivistää prosessin eduiksi ja tuotteen eduiksi.
1. Prosessin etu
- 1) Hieno rakerakenne voidaan saada lisäämättä viljan jauhintaa, mikä eliminoi pylväskiteet ja karkeat dendriitit perinteisessä valussa.
- 2) Matala muovauslämpötila (kuten alumiiniseos voidaan alentaa yli 1200 ℃), mikä voi säästää energiaa.
- 3) Muotin käyttöikää pidennetään. Puolikiinteän lietteen leikkausjännitys alemmassa kiinteässä lämpötilassa on kolme suuruusluokkaa pienempi kuin perinteisen dendriittilietteen, joten täyttö on vakaa, lämpökuorma on pieni ja lämpöväsymislujuus pienenee.
- 4) Vähennä saastumista ja vaarallisia tekijöitä. Päästä eroon korkean lämpötilan nestemäisestä metalliympäristöstä käytön aikana.
- 5) Epämuodostumiskestävyys on pieni ja homogeeninen käsittely voidaan toteuttaa pienellä voimalla ja vaikeasti käsiteltävien materiaalien muodostaminen on helppoa.
- 6) Jähmettymisnopeus kiihtyy, tuottavuus paranee ja prosessisykli lyhenee.
- 7) Se sopii tietokoneavusteiseen suunnitteluun ja valmistukseen, mikä parantaa tuotannon automatisointia.
2. Tuotteen edut
- 1) Osat ovat korkealaatuisia. Kristallirakeiden hienostumisen, tasaisen rakenteen jakautumisen, vähentyneen rungon kutistumisen ja pienemmän lämpöhalkeilutaipumuksen ansiosta matriisin kutistumiskyky poistuu ja mekaaniset ominaisuudet paranevat huomattavasti.
- 2) Jähmettymisen kutistuminen on pieni, joten valetulla rungolla on suuri mittatarkkuus, pieni työstövara ja lähes verkkomuoto.
- 3) Laaja valikoima muoviseoksia. Ei-rautametalliseokset sisältävät alumiinia, magnesiumia, sinkkiä, tinaa, kuparia ja nikkelipohjaisia seoksia; rautapohjaisia seoksia ovat ruostumaton teräs ja vähän seosterästä.
- 4) Metallimatriisikomposiittimateriaalien valmistus. Hyödyntämällä puolikiinteän metallin korkeaa viskositeettia seosten valmistamiseksi, joilla on suuri tiheysero ja pieni kiinteä liukoisuus, se voi myös tehokkaasti sekoittaa eri materiaaleja uusien komposiittimateriaalien valmistamiseksi.
Säilytä tämän artikkelin lähde ja osoite uudelleenpainamista varten: Puolikiinteän metallin valuprosessin historia ja suuntaus
Minghe Die Casting Company ovat omistautuneet valmistukseen ja tarjoavat laadukkaita ja korkean suorituskyvyn valukomponentteja (metalliset painevalukappaleet sisältävät pääasiassa Ohutseinäinen valukappale,Kuuma kamari die casting,Kylmäkammion die casting), Pyöreä palvelu (painevalupalvelu,CNC-työstö,Muotin valmistus, Pintakäsittely) .Jokainen räätälöity alumiinipainevalu, magnesium- tai Zamak / sinkkipainevalu ja muut valutarvikkeet ovat tervetulleita ottamaan yhteyttä meihin.
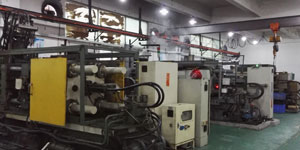
Kaikki prosessit suoritetaan ISO9001: n ja TS 16949: n valvonnassa satojen kehittyneiden painevalukoneiden, 5-akselisten koneiden ja muiden laitteiden kautta, aina blastereista Ultra Sonic -pesukoneisiin. kokeneiden insinöörien, käyttäjien ja tarkastajien tiimi asiakkaan suunnittelun toteuttamiseksi.
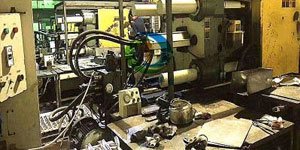
Painevalujen sopimusvalmistaja. Toiminnot sisältävät kylmäkammion alumiinipainevalukappaleet, joiden paino on 0.15 paunaa. 6 lbs., nopea vaihto ja koneistus. Lisäarvopalveluihin kuuluvat kiillotus, tärinä, purseiden poisto, puhallus, maalaus, pinnoitus, päällystys, kokoonpano ja työkalut. Materiaalit, joiden kanssa on työskennelty, sisältävät seoksia, kuten 360, 380, 383 ja 413.
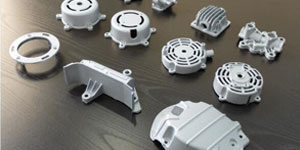
Sinkkipainevalusuunnitteluapu / samanaikaiset suunnittelupalvelut. Mukautettujen sinkkipainevalujen valmistaja. Pienikokoisia valuja, korkeapainevalukappaleita, moniliukuisia muottivaluja, tavanomaisia muottivaluja, yksikkömuotteja ja itsenäisiä muottivaluja ja ontelosuljettuja valukappaleita voidaan valmistaa. Valukappaleita voidaan valmistaa pituudeltaan ja leveydeltään jopa 24 tuumaa +/- 0.0005 tuuman toleranssilla.
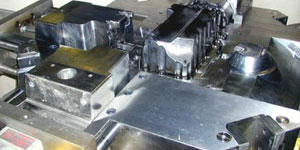
ISO 9001: 2015 -sertifioitu painevaletun magnesiumin valmistaja, ominaisuuksia ovat korkeapaineinen magneettivalumuotoinen valu jopa 200 tonnin kuumakammioon ja 3000 tonnin kylmäkammioon, työkalujen suunnittelu, kiillotus, muovaus, työstö, jauhe- ja nestemaalaus, täydellinen laadunvalvonta CMM-ominaisuuksilla , kokoonpano, pakkaus ja toimitus.
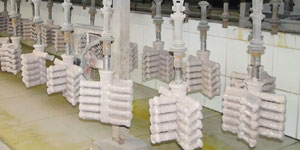
ITAF16949-sertifioitu. Lisävalupalvelu sisältää investointien valu,hiekkavalu,Painovoima valu, Lost vaahto valu,Keskipakovalu,Tyhjö valu,Pysyvä muottien valuKykyihin kuuluvat EDI, tekninen apu, vankka mallinnus ja toissijainen käsittely.
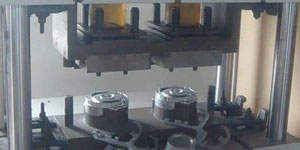
Casting Industries Osatapaustutkimukset: Autot, polkupyörät, lentokoneet, soittimet, vesijetit, optiset laitteet, anturit, mallit, elektroniset laitteet, kotelot, kellot, koneet, moottorit, huonekalut, korut, jigit, tietoliikenne, valaistus, lääkinnälliset laitteet, valokuvauslaitteet, Robotit, veistokset, äänilaitteet, urheiluvälineet, työkalut, lelut ja paljon muuta.
Mitä voimme auttaa sinua tekemään seuraavaksi?
∇ Siirry kotisivulle Die Casting Kiina
→Valuosat- Selvitä, mitä olemme tehneet.
→ Ralated-vinkkejä Die Casting palvelut
By Minghe-painevaluvalmistaja | Luokat: Hyödyllisiä artikkeleita |Materiaali Tunnisteet: Alumiinin valu, Sinkkivalu, Magnesiumvalu, Titaanivalu, Ruostumattoman teräksen valu, Messinkivalu,Pronssivalu,Suoratoista video,Yrityksen historia,Alumiinivalu | Kommentit pois päältä