Jauhemetallurgian (P / M) osien leikkaus
Jauhemetallurgiaprosessin (P / M) käyttö autojen voimajärjestelmien osien valmistuksessa kasvaa edelleen. P / M -prosessilla valmistetuilla osilla on monia tärkeitä ja ainutlaatuisia etuja. Näihin osiin tarkoituksellisesti jätetty huokoinen jäännösrakenne on hyvä itsevoiteluun ja äänieristykseen. Monimutkaisia seoksia, joita on vaikea tai mahdotonta valmistaa perinteisellä valumenetelmällä, voidaan valmistaa käyttämällä P / M -tekniikkaa. Tällä tekniikalla valmistetuilla osilla on yleensä vain vähän tai ei lainkaan käsittelykapasiteettia, mikä tekee niistä halvempia ja vähemmän materiaalihukkaa. Valitettavasti näiden ominaisuuksien vetovoiman takana P / M -osia on vaikea työstää.
Vaikka yksi P / M -teollisuuden alkuperäisistä aikomuksista on poistaa kaikki käsittely, tätä tavoitetta ei ole vielä saavutettu. Useimmat osat voivat olla vain "lähellä lopullista muotoa" ja tarvitsevat vielä viimeistelyä.
Valukappaleisiin ja taotuihin verrattuna pieni määrä materiaalia, joka on poistettava P / M-osista, on kuitenkin tyypillinen kulutusta kestävä materiaali.
Huokoinen rakenne on yksi niistä ominaisuuksista, jotka tekevät p / M -osista monenlaisia käyttötarkoituksia, mutta myös huokoinen rakenne vahingoittaa työkalun käyttöikää. Huokoinen rakenne voi varastoida öljyä ja ääntä, mutta se johtaa myös mikrokatkaisuun. Kun siirrytään edestakaisin reiästä kiinteisiin hiukkasiin, työkalun kärki iskee jatkuvasti, mikä voi johtaa hyvin pieneen väsymismuodon muodonmuutokseen ja hienon reunan romahtamiseen leikkuureunaa pitkin. Mikä pahempaa, hiukkaset ovat yleensä erittäin kovia. Vaikka materiaalin makrokovuus on 20-35 astetta, komponentin hiukkaskoko on jopa 60 astetta. Nämä kovat hiukkaset aiheuttavat kovaa ja nopeaa reunan kulumista. Monet p / M -osat ovat lämpökäsiteltäviä, ja materiaalin kovuus ja lujuus ovat korkeammat lämpökäsittelyn jälkeen. Sintraus- ja lämpökäsittelytekniikan sekä käytettyjen kaasujen ansiosta materiaalin pinta sisältää kovia ja kulutusta kestäviä oksideja ja / tai karbideja.
P / M -osien suorituskyky
Suurin osa P / M -osien ominaisuuksista, mukaan lukien työstettävyys, liittyvät paitsi seoksen kemialliseen koostumukseen myös huokoisen rakenteen huokoisuuteen. Monien rakenneosien huokoisuus on jopa 15% - 20%. Suodatuslaitteina käytettävien osien huokoisuus voi olla jopa 50%. Sarjan toisessa päässä väärennettyjen tai lonkkaosien huokoisuus on vain 1% tai vähemmän. Näistä materiaaleista on tulossa erityisen tärkeitä auto- ja lentokoneen sovelluksissa, koska ne voivat saavuttaa korkeamman lujuuden.
P / M -seoksen vetolujuus, sitkeys ja sitkeys lisääntyvät tiheyden kasvaessa, ja myös työstettävyyttä voidaan parantaa, koska huokoisuus on haitallista työkalun kärjelle.
Huokoisuuden lisääntyminen voi parantaa osien äänieristyskykyä. Vakio -osien vaimennusvärähtely pienenee merkittävästi P / M -osissa, mikä on erittäin tärkeää työstökoneille, ilmastointipuhallusputkille ja pneumaattisille työkaluille. Suuri huokoisuus on välttämätöntä myös itsevoiteleville vaihteille.
Vaikeudet koneistuksessa
Vaikka yksi P / M-teollisuuden jatkuvan kehityksen tavoitteista on työstön poistaminen, ja yksi P / M-prosessin tärkeimmistä vetovoimista on se, että tarvitaan vain pieni määrä käsittelyä, monet osat tarvitsevat edelleen jälkikäsittelyä saadakseen suurempi tarkkuus tai parempi pintakäsittely. Valitettavasti näiden osien työstäminen on erittäin vaikeaa. Suurin osa ongelmista johtuu huokoisuudesta. Huokoisuus johtaa leikkuuterän mikroväsymykseen. Terä leikkaa jatkuvasti sisään ja ulos. Se kulkee hiukkasten ja reikien välillä. Toistuva pieni isku johtaa pieniin halkeamiin leikkuureunassa.
Nämä väsymyshalkeamat kasvavat, kunnes leikkuureuna romahtaa. Tämäntyyppinen mikrosirun reuna on yleensä hyvin pieni, ja siinä on yleensä normaalia hankaavaa kulumista.
Huokoisuus vähentää myös P / M -osien lämmönjohtavuutta, mikä johtaa korkeaan lämpötilaan leikkuuterässä ja aiheuttaa kraatterin kulumista ja muodonmuutoksia. Sisäisesti kytketty huokoinen rakenne tarjoaa polun leikkuunesteen poistamiseksi leikkuualueelta. Tämä voi aiheuttaa kuumia halkeamia tai muodonmuutoksia erityisesti porauksessa.
Sisäisen huokoisen rakenteen aiheuttama pinta -alan kasvu johtaa myös hapettumiseen ja / tai hiiltymiseen lämpökäsittelyn aikana. Kuten aiemmin mainittiin, nämä oksidit ja karbidit ovat kovia ja kulutusta kestäviä.
Huokoinen rakenne aiheuttaa myös osan kovuuslukeman epäonnistumisen, mikä on erittäin tärkeää. Kun P / M -osan makrokovuus mitataan tarkoituksellisesti, se sisältää reiän kovuuskertoimen. Huokoinen rakenne johtaa rakenteen romahtamiseen ja antaa väärän vaikutelman suhteellisen pehmeistä osista. Hiukkaset ovat paljon kovempia. Kuten edellä on kuvattu, ero on dramaattinen.
Sulkemisten olemassaolo PM -osissa on myös epäedullista. Koneistuksen aikana nämä hiukkaset vedetään ylös pinnalta ja naarmu tai naarmu muodostuu kappaleen pintaan, kun sitä hierotaan työkalun eteen. Nämä sulkeumat ovat yleensä suuria, jättäen näkyviin reikiä osan pintaan.
Hiilipitoisuuden ero johtaa työstettävyyden epäjohdonmukaisuuteen. Esimerkiksi fc0208 -seoksen hiilipitoisuus vaihtelee välillä 0.6% - 0.9%. Erä materiaaleja, joissa on 0.9% hiilipitoisuutta, ovat suhteellisen kovia, mikä johtaa huonoon käyttöikään. Toisen materiaalierän, jonka hiilipitoisuus on 0.6%, käyttöikä on erinomainen. Molemmat seokset ovat sallittujen rajojen sisällä.
Viimeinen koneistusongelma liittyy P / M -osan leikkaustyyppiin. Koska osa on lähellä lopullista muotoa, leikkuusyvyys on yleensä hyvin matala. Tämä vaatii vapaan leikkausreunan. Lastujen kertyminen leikkuureunaan johtaa usein mikrohakeeseen.
Jalostustekniikka
Näiden ongelmien ratkaisemiseksi käytetään useita (teollisuudelle ainutlaatuisia) tekniikoita. Pinnan huokoinen rakenne tiivistyy usein tunkeutumalla. Yleensä tarvitaan lisäleikkausta. Viime aikoina on käytetty parempia jauheenvalmistustekniikoita, jotka on suunniteltu lisäämään jauheen puhtautta ja vähentämään oksideja ja karbideja lämpökäsittelyn aikana.
Suljetun pinnan huokoinen rakenne saavutetaan metallin (yleensä kuparin) tai polymeerin tunkeutumisella. On spekuloitu, että tunkeutuminen toimii voiteluaineena. Suurin osa kokeellisista tiedoista osoittaa, että todellinen etu on pinnan huokoisen rakenteen sulkeminen ja siten leikkaavan reunan mikroväsymyksen estäminen. Naarmuuntumisen vähentäminen parantaa työkalun käyttöikää ja pinnan viimeistelyä. Dramaattisin tunkeutumisen käyttö osoittaa 200% pidemmän työkalun käyttöiän, kun huokoinen rakenne on suljettu.
Lisäaineiden, kuten MNS, s, MoS2, MgSiO3 ja BN, tiedetään pidentävän työkalun käyttöikää. Nämä lisäaineet parantavat työstettävyyttä helpottamalla lastujen erottumista työkappaleesta, rikkomaten lastuja, estäen lastujen kerääntymistä ja voitelemalla leikkuureunaa. Lisäaineiden määrän lisääminen voi parantaa työstettävyyttä, mutta vähentää lujuutta ja sitkeyttä.
Jauheen sumutustekniikka sintraus- ja lämpökäsittelyuunikaasun hallitsemiseksi mahdollistaa puhtaan jauheen ja osien valmistuksen, mikä minimoi sulkeumien ja pinnan oksidikarbidien esiintymisen.
Työkalumateriaali
P / M-teollisuudessa yleisimmin käytettyjä työkaluja ovat materiaalit, jotka ovat kulutusta kestäviä, reunahalkeamattomia ja halkeamattomia hyvän pinnan viimeistelyolosuhteissa. Nämä ominaisuudet ovat hyödyllisiä kaikissa koneistustöissä, erityisesti P / M -osissa. Tähän luokkaan kuuluvat työkalumateriaalit ovat kuutiometriset boorinitridityökalut (CBN), päällystämättömät ja päällystetyt kermetit sekä parannetut pinnoitetut sintratut kovametallit.
CBN -työkalut ovat houkuttelevia korkean kovuuden ja kulutuskestävyytensä vuoksi. Tätä työkalua on käytetty monta vuotta teräksen ja valuraudan käsittelyssä, jonka Rockwell -kovuus on 45 ja enemmän. P / M -seoksen ainutlaatuisten ominaisuuksien sekä mikro- ja makrokovuuden välisen merkittävän eron vuoksi CBN -työkaluja voidaan käyttää P / M -osiin, joiden Rockwell -kovuus on 25. Avainparametri on hiukkasten kovuus. Kun hiukkasten kovuus ylittää Rockwellin 50 astetta, CBN -työkaluja on saatavana makron kovuusarvosta riippumatta. Näiden työkalujen ilmeinen rajoitus on niiden sitkeyden puute. Ajoittaisen leikkauksen tai suuren huokoisuuden tapauksessa reunojen vahvistaminen, mukaan lukien negatiiviset viistot ja raskas hionta, on tarpeen. Yksinkertainen kevyt leikkaus voidaan tehdä hiotulla leikkuureunalla.
CBN: stä on useita tehokkaita materiaaleja. Paras sitkeysmateriaali koostuu pääasiassa koko CBN: stä. Niillä on erinomainen sitkeys, joten niitä voidaan käyttää rouhintaan. Niiden rajoitukset liittyvät yleensä pinnan viimeistelyyn. Sen määräävät suurelta osin yksittäiset CBN -hiukkaset, jotka muodostavat työkalun. Kun hiukkaset putoavat leikkuureunasta, ne vaikuttavat työkappaleen materiaalin pintaan. Ei kuitenkaan ole niin vakavaa, että pienhiukkastyökalu putoaa yhdestä hiukkasesta.
Yleensä käytetyssä CBN -materiaalissa on korkea CBN -pitoisuus ja keskikokoinen hiukkaskoko. CBN -viimeistelyterä on hienorakeista ja CBN -pitoisuus on alhainen. Ne ovat tehokkaimpia, kun vaaditaan kevyttä leikkausta ja pintakäsittelyä tai kun käsiteltävä seos on erityisen kova.
Monissa leikkaussovelluksissa työkalun käyttöikä on riippumaton materiaalityypistä. Toisin sanoen mikä tahansa CBN -materiaali voi saavuttaa samanlaisen käyttöiän. Näissä tapauksissa materiaalin valinta perustuu pääasiassa kunkin leikkuuterän halvimpiin kustannuksiin. Yhdellä pyöreällä terällä on koko CBN -yläpinta ja siinä voi olla neljä tai useampia leikkuureunoja, mikä on halvempaa kuin neljä upotettua CBN -terää.
Kun P / M -osien kovuus on pienempi kuin Rockwell 35 astetta ja hiukkasten kovuus on alueella, kermetti on yleensä yksi vaihtoehdoista. Kermetit ovat erittäin kovia, voivat tehokkaasti estää sirun kertymisen ja kestävät suurta nopeutta. Lisäksi koska kermetit ovat aina olleet käytössä teräksen ja ruostumattoman teräksen nopeassa ja viimeistelykoneistuksessa, niissä on yleensä ihanteelliset geometriset urat, jotka sopivat lähellä muodostettuja osia.
Nykyiset kermetit ovat monimutkaisia metallurgiassa, ja niissä on jopa 11 seosaineita. Ne sintrataan yleensä TiCN -hiukkasista ja Ni Mo -liimasta. TiCN tarjoaa kovuutta, lastukertymiskestävyyttä ja kemiallista vakautta, jotka ovat tärkeitä kermetien onnistuneelle käytölle. Lisäksi näillä työkaluilla on yleensä korkea liimapitoisuus, mikä tarkoittaa, että niillä on hyvä sitkeys. Sanalla sanoen niillä on kaikki P / M -seoksen tehokkaan käsittelyn ominaisuudet. Monenlaiset kermetit ovat tehokkaita, aivan kuten sintrattu volframikarbidisementoitu karbidi, mitä korkeampi sideaineen pitoisuus, sitä parempi sitkeys.
Tunnettu suhteellisen uusi kehitys on, että keskilämpötilainen kemiallinen höyrystys (mtcvd) tarjoaa myös edun P / M -teollisuudelle. Mtcvd säilyttää perinteisen kemiallisen höyrysaostamisen (CVD) kaikki kulutuksen ja kraatterin kulutuskestävyyden, mutta parantaa myös sitkeyttä objektiivisesti. Sitkeyden kasvu johtuu pääasiassa halkeamien vähenemisestä. Pinnoite kerrostetaan korkeassa lämpötilassa ja jäähdytetään sitten uunissa. Pinnoite sisältää halkeamia, kun työkalu saavuttaa huonelämpötilan epäjohdonmukaisen lämpölaajenemisen vuoksi. Samoin kuin tasolasin naarmut, nämä halkeamat vähentävät leikkaavan reunan lujuutta. Mtcvd: n alempi laskeutumislämpötila johtaa pienempään halkeamistiheyteen ja leikkuuterän parempaan sitkeyteen.
Kun CVD -pinnoitteen ja mtcvd -pinnoitteen alustalla on samat ominaisuudet ja reunasidos, niiden sitkeyden ero voidaan osoittaa. Käytettäessä sovelluksissa, joissa vaaditaan reunakestävyyttä, mtcvd -pinnoitteen suorituskyky on parempi kuin CVD -pinnoitteen. Analyysin avulla, kun työstetään huokoisen rakenteen omaavia P / M -osia, reunan sitkeys on tärkeää. Mtcvd -pinnoite on parempi kuin CVD -pinnoite.
Fyysinen höyrystyspinnoite (PVD) on ohuempi ja vähemmän kulutusta kestävä kuin mtcvd- tai CVD -pinnoite. PVD -pinnoite voi kuitenkin kestää merkittäviä vaikutuksia sovelluksessa. PVD -pinnoite on tehokas, kun leikkaus on hankaavaa kulumista, CBN ja kermetit ovat liian hauraita ja edellyttävät erinomaista pinnan viimeistelyä.
Esimerkiksi C-2-sementoidun karbidin leikkaava reuna voidaan työstää fc0205 linjanopeudella 180 m / min ja syöttönopeudella 0.15 mm / kierros. 20 osan työstön jälkeen lastujen kertyminen voi aiheuttaa mikro-romahtamisen. Kun käytetään PVD-titaaninitridipinnoitetta (TIN), lastujen kertyminen estyy ja työkalun käyttöikä pitenee. Kun tässä testissä käytetään tinapinnoitetta, P / M -osien kulutusominaisuuksien odotetaan olevan tehokkaampia TiCN -pinnoitteen kanssa. TiCN: llä on melkein sama sirun kertymisen kestävyys kuin tinalla, mutta se on kovempaa ja kulutusta kestävämpää kuin tina.
Huokoinen rakenne on tärkeä ja vaikuttaa fc0208 -seoksen työstettävyyteen. Kun huokoinen rakenne ja ominaisuudet muuttuvat, eri työkalumateriaalit tarjoavat vastaavia etuja. Kun tiheys on pieni (6.4 g/cm3), makrokovuus on alhainen. Tässä tapauksessa mtcvd -pinnoitettu kovametalli tarjoaa parhaan käyttöiän. Leikkuuterän mikroväsymys on erittäin tärkeää, ja reunan sitkeys on erittäin tärkeää. Tässä tapauksessa hyvä sitkeyskermetiterä tarjoaa maksimaalisen käyttöiän.
Tuotettaessa samaa seosta, jonka tiheys on 6.8 g / cm3, hankauskulumisesta tulee tärkeämpää kuin reunahalkeamasta. Tässä tapauksessa mtcvd -pinnoite tarjoaa parhaan käyttöiän. PVD -pinnoitettua kovametallia käytetään kahden erittäin kovan osan testaamiseen, ja se rikkoutuu, kun se koskettaa leikkuureunaa.
Kun nopeus kasvaa (lineaarinen nopeus on yli 300 metriä minuutissa), kermetit ja jopa pinnoitetut kermetit aiheuttavat kraatterin kulumista. Päällystetty kovametalli on sopivampi, varsinkin kun päällystetyn kovametallin leikkuureunan sitkeys on hyvä. Mtcvd -pinnoite on erityisen tehokas kovetetulle kovametallille, jolla on runsaasti kobolttia.
Kermettejä käytetään yleisimmin sorvauksessa ja porauksessa. PVD-pinnoitetut sementtikarbidit ovat ihanteellisia kierteen työstöön, koska pienempiä nopeuksia ja enemmän huomiota rakentamiseen voidaan odottaa.
Säilytä tämän artikkelin lähde ja osoite uudelleenpainamista varten:Jauhemetallurgian (P / M) osien leikkaus
Minghe Casting Company on omistautunut valmistukseen ja tarjoaa laadukkaita ja korkean suorituskyvyn valuosia (metalliset painevalukappaleet sisältävät pääasiassa Ohutseinäinen valukappale,Kuuma kamari die casting,Kylmäkammion die casting), Pyöreä palvelu (painevalupalvelu,CNC-työstö,Muotin valmistus, Pintakäsittely) .Jokainen räätälöity alumiinipainevalu, magnesium- tai Zamak / sinkkipainevalu ja muut valutarvikkeet ovat tervetulleita ottamaan yhteyttä meihin.
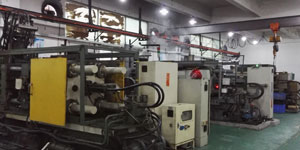
Kaikki prosessit suoritetaan ISO9001: n ja TS 16949: n valvonnassa satojen kehittyneiden painevalukoneiden, 5-akselisten koneiden ja muiden laitteiden kautta, aina blastereista Ultra Sonic -pesukoneisiin. kokeneiden insinöörien, käyttäjien ja tarkastajien tiimi asiakkaan suunnittelun toteuttamiseksi.
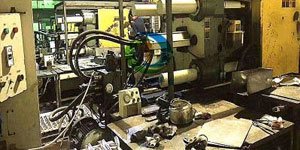
Painevalujen sopimusvalmistaja. Toiminnot sisältävät kylmäkammion alumiinipainevalukappaleet, joiden paino on 0.15 paunaa. 6 lbs., nopea vaihto ja koneistus. Lisäarvopalveluihin kuuluvat kiillotus, tärinä, purseiden poisto, puhallus, maalaus, pinnoitus, päällystys, kokoonpano ja työkalut. Materiaalit, joiden kanssa on työskennelty, sisältävät seoksia, kuten 360, 380, 383 ja 413.
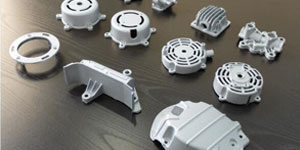
Sinkkipainevalusuunnitteluapu / samanaikaiset suunnittelupalvelut. Mukautettujen sinkkipainevalujen valmistaja. Pienikokoisia valuja, korkeapainevalukappaleita, moniliukuisia muottivaluja, tavanomaisia muottivaluja, yksikkömuotteja ja itsenäisiä muottivaluja ja ontelosuljettuja valukappaleita voidaan valmistaa. Valukappaleita voidaan valmistaa pituudeltaan ja leveydeltään jopa 24 tuumaa +/- 0.0005 tuuman toleranssilla.
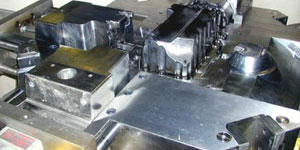
ISO 9001: 2015 -sertifioitu painevaletun magnesiumin valmistaja, ominaisuuksia ovat korkeapaineinen magneettivalumuotoinen valu jopa 200 tonnin kuumakammioon ja 3000 tonnin kylmäkammioon, työkalujen suunnittelu, kiillotus, muovaus, työstö, jauhe- ja nestemaalaus, täydellinen laadunvalvonta CMM-ominaisuuksilla , kokoonpano, pakkaus ja toimitus.
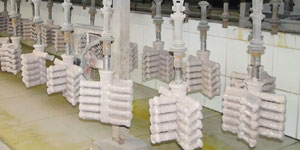
ITAF16949-sertifioitu. Lisävalupalvelu sisältää investointien valu,hiekkavalu,Painovoima valu, Lost vaahto valu,Keskipakovalu,Tyhjö valu,Pysyvä muottien valuKykyihin kuuluvat EDI, tekninen apu, vankka mallinnus ja toissijainen käsittely.
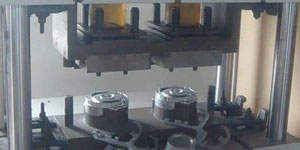
Casting Industries Osatapaustutkimukset: Autot, polkupyörät, lentokoneet, soittimet, vesijetit, optiset laitteet, anturit, mallit, elektroniset laitteet, kotelot, kellot, koneet, moottorit, huonekalut, korut, jigit, tietoliikenne, valaistus, lääkinnälliset laitteet, valokuvauslaitteet, Robotit, veistokset, äänilaitteet, urheiluvälineet, työkalut, lelut ja paljon muuta.
Mitä voimme auttaa sinua tekemään seuraavaksi?
∇ Siirry kotisivulle Die Casting Kiina
→Valuosat- Selvitä, mitä olemme tehneet.
→ Ralated-vinkkejä Die Casting palvelut
By Minghe-painevaluvalmistaja | Luokat: Hyödyllisiä artikkeleita |Materiaali Tunnisteet: Alumiinin valu, Sinkkivalu, Magnesiumvalu, Titaanivalu, Ruostumattoman teräksen valu, Messinkivalu,Pronssivalu,Suoratoista video,Yrityksen historia,Alumiinivalu | Kommentit pois päältä