Eri tekijät, jotka vaikuttavat sijoitusvalujen mittojen vakauteen
Investointivalujen mittojen tarkkuuden jatkuva parantaminen ja ylisuurten aiheuttamien jätteiden vähentäminen on aina ollut yksi investointivalutyöntekijöiden tärkeimmistä tavoitteista kotimaassa ja ulkomailla.
1. Sijoitusvalujen mittainen vakaus
1. Vahamallin ja sen vaikuttavien tekijöiden mittapysyvyys
Useimmissa tapauksissa vahamuotin koko vaihtelee suuresti, kun valukoko vaihtelee, ja on muutamia poikkeuksia. Kaiken kaikkiaan vahamuotin koon vaihtelu muodostaa 10-70% valun kokovaihtelusta.
Valuprosessin parametrit vaikuttavat ratkaisevasti vahamuotin mittatarkkuuteen. Tärkeimmät tekijät ovat seuraavat:
(1) Vahan puristuslämpötila
Eri muovausmateriaaleilla on erilaiset suorituskyvyt vahan puristuslämpötilan vaikutuksesta. Kun käytetään vahapohjaisia muovausmateriaaleja, vahan puristuslämpötila on hyvin herkkä vahamuotin mittatarkkuuden vaikutukselle, kun taas hartsipohjaisilla muovausmateriaaleilla on vähemmän vaikutusta.
(2) Ruiskutuspaine
Kun paine on pieni, vahamuotin kutistumisnopeus laskee merkittävästi paineen kasvaessa. Kuitenkin sen jälkeen, kun painetta on nostettu jossain määrin (≥ 1.6 MPa), paineella ei ole juuri mitään vaikutusta vahamuotin kokoon. Ei ole ihme, että ulkomaiset testitulokset johtavat usein siihen, että "paineella ei ole mitään tekemistä vahamuotin koon kanssa", mutta monien kotimaisten yritysten vaikutelma ei ole täysin sama.
(3) Virtausnopeus
Muotimateriaalin virtausnopeutta voidaan muuttaa seuraavilla kahdella tavalla, mutta vaikutus vahamuotin kokoon ei ole sama:
· Muuttamalla vahapuristimen virtausnopeuden asetusta tällä menetelmällä on vain vähän vaikutusta vahamuotin kutistumiseen. Sillä on kuitenkin tärkeä vaikutus monimutkaisten muotoisten ohutseinäisten osien tai ytimien vahamuotojen täyttymiseen ja pinnan laatuun.
· Tällä menetelmällä on suuri vaikutus muuttamalla vahan ruiskutusportin poikkileikkausaluetta, koska vahan ruiskutusportin poikkileikkauspinnan lisääminen voi paitsi alentaa vahan puristuslämpötilaa myös pidentää jähmettymistä muotimateriaalin aika vaharuiskutusportissa, mikä lisää vahamuotin tiivistymistä. Kutistumisaste ja pinnan kutistuminen vähenevät.
(4) Injektioaika
Ns. Ruiskutusaika sisältää kolme täyttö-, tiivistys- ja ylläpitoaikaa. Täyttöaika viittaa aikaan, jolloin muovausmateriaali täyttää muovausontelon; tiivistys viittaa aikaan valun täyttämisestä vahan ruiskutussuuttimen sulkemiseen; ja pito viittaa aikaan vahan ruiskutussuuttimen sulkemisesta muotin ulostuloon.
Ruiskutusajalla on merkittävä vaikutus vahamuotin kutistumisnopeuteen. Tämä johtuu siitä, että onteloon voidaan puristaa lisää muotimateriaalia lisäämällä ruiskutusaikaa ja vahamuotti tiivistyy enemmän, mikä pienentää kutistumisnopeutta. Vahamallin paino kasvaa pidemmän tiivistysajan myötä. Tiivistymisajan tulisi olla sopiva. Jos tiivistysaika on liian pitkä, vaharuiskutusportin muotimateriaali on täysin kiinteytynyt eikä tiivistys toimi. Kuvasta 4 voidaan myös nähdä, että kun ruiskutusaika on lyhyt (15-25 s), vahan puristuslämpötila nousee ja kutistumisnopeus kasvaa; mutta kun ruiskutusaikaa pidennetään 25-35 sekuntiin (olettaen, että täyttöaika pysyy vakiona, todellinen Edellä mainittu on tiivistysajan pidentäminen) Vahan puristuslämpötilan vaikutus pienenee; kun ruiskutusaika kasvaa yli 35 sekuntiin, tapahtuu päinvastainen tilanne, eli kun vahan puristuslämpötila nousee, vahamuotin kutistumisnopeus pienenee sen sijaan. Tämä ilmiö voidaan selittää sillä, että muotimateriaalin lämpötilan nostamisella ja tiivistysajan pidentämisellä on sama vaikutus kuin vahamuotin tiivistymisasteen lisäämisellä.
(5) Muovauslämpötila ja vahapuristuslaitteet
Muovauslämpötila on korkea, vahamuotti jäähtyy hitaasti ja kutistumisnopeus kasvaa. Tämä johtuu siitä, että vahamuotti on edelleen puristusmuovissa ennen muotin poistamista, ja kutistuminen on rajoitettua, mutta muotin poistamisen jälkeen se kutistuu vapaasti. Siksi, jos vahamuotin lämpötila on korkea, kun muotti vapautetaan, lopullinen kutistumisnopeus on suuri ja päinvastoin, kutistumisnopeus on pieni.
Samalla tavalla vahapuristimen jäähdytysjärjestelmä voi vaikuttaa noin 0.3% vahamuotin kokoon.
Lopuksi on syytä korostaa, että kun käytetään vahapohjaisia muotimateriaaleja, vahatahna on kolmivaiheinen rinnakkaiselojärjestelmä kiinteästä, nesteestä ja kaasusta. Kolmen faasin tilavuussuhteella on suuri vaikutus vahamuotin kokoon. Näiden kolmen välistä suhteellista suhdetta ei voida kontrolloida todellisessa tuotannossa, mikä on myös tärkeä syy vahapohjaisia muovausmateriaaleja käyttävien vahamuottien heikkoon mittatarkkuuteen.
2. Kuorimateriaalin ja kuorenvalmistusprosessin vaikutus valujen mittatarkkuuteen
Muotin kuoren vaikutus valukappaleeseen johtuu pääasiassa muotin kuoren lämpölaajenemisesta ja muodonmuutoksesta (korkean lämpötilan viruminen) polttamisen aikana sekä muotin kuoren rajoittumisesta (tukkeutumisesta) valu.
(1) Kuoren lämpölaajeneminen
Riippuu lähinnä kuoren materiaalista. Eri tulenkestävillä materiaaleilla on erilaiset laajentumisnopeudet. Yleisesti käytetyistä tulenkestävistä materiaaleista pienin paisuntasuhde on sulatetulla piidioksidilla, jota seuraa alumiinisilikaatti, ja piidioksidi on suurin ja epätasainen. Testin jälkeen määritetään, että alumiinisilikaattikuori voidaan lämmittää huoneenlämpötilasta 1000 ℃: een, kuori voi tuottaa noin 0.25%: n paisumisen, mikä on pieni osa valukokon kutistumisesta. Siksi, jos käytetään tällaisia tulenkestäviä materiaaleja, sen kuori on paremman mittapysyvyyden omaava, kuten sulatettu piidioksidi on epäilemättä parempi. Kuitenkin, jos käytetään piidioksidia, kuoren koko vaihtelee suuresti.
(2) Terminen muodonmuutos (korkean lämpötilan viruminen)
Esimerkiksi kuorella, joka käyttää sideaineena vesilasia, on huomattavasti suurempi virumisaste korkeissa lämpötiloissa yli 1000 ° C kuin piidioksidisoolilla ja etyylisilikaattikuorilla. Vaikka itse sulatetulla korundilla on korkea tulenkestävyys, epäpuhtauksien, kuten natriumoksidin, läsnäolon vuoksi kuoren polttolämpötila, joka on korkeampi kuin 1000 ℃, voi myös aiheuttaa ryömiä, mikä johtaa heikkoon mittatarkkuuteen.
(3) Muotin kuoren pidätys valun kutistumisessa - muotin kuoren vetäytyminen ja kokoonpuristuminen Tämä riippuu myös pääasiassa muotin kuoren materiaalista.
Yhteenvetona voidaan todeta, että tulenkestävillä materiaaleilla on suuri merkitys kuoren vaikutuksessa valun kokovaihteluun, mutta sideaineen roolia ei voida jättää huomiotta. Sitä vastoin kuorenvalmistusprosessin vaikutus on pieni.
3. Valujen epätasaisen jäähdytyksen aiheuttaman jännityksen vaikutus mittojen vakauteen
Valun kunkin osan jäähdytysnopeus (porttijärjestelmä mukaan lukien) on erilainen, mikä aiheuttaa lämpöjännitystä ja vääristää valua, mikä vaikuttaa mittojen vakauteen. Tämä tapahtuu usein varsinaisessa tuotannossa. Valujen jäähdytysnopeuden vähentäminen ja juoksijoiden yhdistelmän parantaminen ovat tehokkaita ennaltaehkäiseviä toimenpiteitä.
2. Avain tarkkuuden parantamiseen-muotin kutistumisnopeus on määritetty oikein
Edellä mainittu "mittatarkkuus" eroaa "mittatarkkuudesta" ja "tarkkuudesta (tarkkuudesta)". Mittapysyvyys (eli tarkkuus) on synonyymi mittajohdonmukaisuudelle, joka heijastaa mitan vaihtelun tai hajonnan asteen, ja se mitataan yleensä keskihajonnalla σ. Suurin syy mittojen epävakauteen on löysä prosessinhallinta, joka on satunnainen virhe. Tarkkuus viittaa siihen, missä määrin monien mitattujen arvojen aritmeettinen keskiarvo poikkeaa nimelliskoosta tietyn koon valussa, eli keskimääräisen poikkeaman koosta. Investointivalussa tärkein syy huonoon mittatarkkuuteen on kutistumisnopeuden virheellinen kohdistaminen profilointisuunnittelun aikana, mikä on järjestelmällinen virhe, jota yleensä säädetään korjaamalla muotti toistuvasti. Mittatarkkuus (tarkkuus) on edellä mainittujen kahden yhdistelmä. Siksi valujen mittatarkkuuden parantamiseksi ja tuotteen kokotoleranssien ongelman ratkaisemiseksi prosessia on valvottava tiukasti mittojen vaihtelun vähentämiseksi, mutta myös valun jokaisen ulottuvuuden kutistumisnopeus on määritettävä oikein profiilia suunniteltaessa .
On tunnettua, että tarkkuusvalujen lopullinen kokonaiskutistuminen on yhdistelmä vahamuotista, seoksen kutistumisesta ja pienestä määrästä kuoren laajentumista. Kuori turpoaa noin 0.25%ja sen vaikutus on rajallinen. Vaikka seoksen lineaarinen kutistumisnopeus on usein suurempi kuin vahamuotin, vahapuristusprosessin aiheuttamilla mittavaihteluilla on suurempi vaikutus. Muotin korjauskustannusten alentamiseksi ja valukoon vaihtelun vähentämiseksi on erittäin tärkeää hallita vahamuotin kutistumisnopeutta.
1. Vahamuotin kutistuminen
Vahamuotin kutistuminen on mitattava sen jälkeen, kun vahamuotin koko on täysin vakiintunut. Tämä johtuu siitä, että vahamuotin kutistuminen ei pysähdy kokonaan muotin poistamisen jälkeen. Vahamuotin koko vakautuu toisinaan vain muutaman päivän kuluttua muotin poistamisesta. Suurin osa muotimateriaalin kutistumisesta on kuitenkin periaatteessa valmis yhden tai usean tunnin kuluessa muotin poistamisesta. Vahamuotin kutistumisnopeudella on pääasiassa seuraavat vaikuttavat tekijät:
(1) Muotimateriaalin tyyppi;
(2) vahamallin leikkauskoko;
On syytä korostaa, että vahamuotin poikkileikkauksella on merkittävä vaikutus kutistumisnopeuteen. Esimerkiksi tyypillisen täyttämättömän muotimateriaalin kutistumisnopeus puristettaessa eri paksuisia vahamuotteja. Vahamuotin osan paksuuden ei pitäisi yleensä ylittää 13 mm. Kun paksuus on suurempi kuin 13 mm, seinämän paksuutta voidaan pienentää käyttämällä kylmiä vahalohkoja tai metallisydämiä kutistumisen vähentämiseksi, mikä on erityisen tärkeää ei-täyteaineille.
Huomautus: 1. Vesiliukoisen muotimateriaalin kutistumisnopeus on noin 0.25%;
2. Kun käytetään liukoisia ytimiä, keraamisia ytimiä tai kvartsilasiputkia, vahamuotin lineaarista kutistumista ei tapahdu ytimen kanssa;
(3) Ydintyypit
Vahamuotin ontelon koko on epäilemättä ytimen muodon mukainen. Siksi ytimien käytöstä on tullut tapa parantaa vahamuotin ontelon mittatarkkuutta.
2. Metalliseoksen kutistuminen
Metalliseoksen kutistuminen riippuu pääasiassa seuraavista tekijöistä:
· Valulejeeringin tyyppi ja kemiallinen koostumus;
· Valugeometria (mukaan lukien rajoitustila ja leikkauskoko);
· Valuparametrit, kuten kaatolämpötila, kuoren lämpötila, valujäähdytys jne.;
· Keraamisten ytimien, kvartsilasiputkien jne. Käyttö
Koska kaatolämpötilaa, kuoren lämpötilaa, valujäähdytysnopeutta ja muita prosessiparametreja valvotaan yleensä tiukasti standardiprosessikorteilla tuotantoprosessin aikana, tämän aiheuttamat kokovaihtelut eivät ole suuria eri tuotantoerien välillä. Vaikka kaatolämpötila ylittää prosessin spesifikaation edellyttämän alueen, valukoon vaihtelu ei yleensä ole suuri. Samoin kuin vahamuotti, valun leikkauskoko ja muotin kuoren rajoitukset ovat tärkeimmät tekijät, jotka vaikuttavat seoksen kutistumiseen. Kokemus osoittaa, että täysin rajoitetun koon kutistumisnopeus on 85–89% vapaakutistumisasteesta; puolirajoitettu koko on 94-95%.
3. Ensimmäisen mittausnäyte -erän vähimmäismäärä
Edellä lueteltu kutistumisnopeus on aiempien kokemusten perusteella saatuja empiirisiä tietoja, ei todellinen kutistumisnopeus. Suunnittele ja valmista muotit näiden tietojen perusteella, korjaus on väistämätöntä. Korjausten tarkkuuden ja onnistumisprosentin parantamiseksi ja korjausten määrän vähentämiseksi keskeinen linkki on tarkistaa riittävän määrän koevalunäytteiden koko huolellisesti. Koska valmistamiemme valujen koko ei voi olla täsmälleen sama, joten vain silloin, kun mitattujen näytteiden määrä on riittävän suuri, saatu keskimääräinen arvo voi olla lähellä todellista aritmeettista keskiarvoa. Tästä ei ole vaikeaa nähdä, että mittausnäytteiden vähimmäismäärä liittyy suoraan tuotantoprosessin prosessikykyyn hallita tuotteen koon johdonmukaisuutta (prosessikyky). Jos valukappaleet ovat kooltaan täysin samat, vain yksi näyte on testattava; Päinvastoin, jos valukoko vaihtelee suuresti,
On tarpeen mitata paljon näytteitä tarkempien kutistumistietojen saamiseksi. Kuten aiemmin mainittiin, tuotantoprosessin kykyä hallita kokoa voidaan esittää tämän prosessin tuottaman valukoon 6σ. Useimpien investointivalimoiden nykyisestä teknologisesta tasosta Hp on enimmäkseen yli 0.5, joten ensimmäinen erä mittausnäytteitä vaatii yleensä vähintään 11 näytettä.
kolme. Mittausjärjestelmän analyysi
Analysoitaessa ja ratkaistaessa tuotteen kokoongelmia meidän on kiinnitettävä huomiota käytetyn mittausjärjestelmän tarkkuuteen ja luotettavuuteen. Mittauslaitteiden ja laitteiden usein tapahtuvan kalibroinnin lisäksi on myös tärkeää minimoida mittausvirheet. Jos mittausjärjestelmässä (mukaan lukien käyttäjä ja toimintatapa) on suuri virhe, hylätyt aineet voidaan katsoa päteviksi tuotteiksi, mutta myös monia päteviä tuotteita voidaan arvioida hylätyiksi, mikä voi aiheuttaa suuria onnettomuuksia tai tarpeetonta taloudellista tappiot. Helpoin tapa määrittää, soveltuuko mittausjärjestelmä tiettyyn mittaustehtävään, on suorittaa toistettavuuden ja toistettavuuden kelpoisuustestit. Ns. Toistettavuus tarkoittaa sitä, että sama tarkastaja käyttää samaa laitetta (tai laitetta) ja menetelmää saman osan tarkastamiseen ja tulosten johdonmukaisuuden saavuttamiseen. Toistettavuus viittaa tulosten yhdenmukaisuuteen, jonka eri toimijat ovat saaneet käyttämällä eri instrumentteja saman osan tarkistamiseen. Amerikkalainen autoteollisuuden toimintaryhmä (Automotive Industry Action Group) määrää, että toistettavuuden ja toistettavuuden tutkimus- ja kehitystyön integroidun keskihajonnan prosenttiosuus mitattujen valukokovaihteluiden keskihajonnasta on ≤30% standardina mittausjärjestelmän täyttämiseksi. vaatimukset [5]. Joidenkin suurikokoisten ja monimutkaisten valujen mittauksessa kaikki mittausjärjestelmät eivät voi täyttää tätä vaatimusta. Sallitun mittausvirheen muotteja mitattaessa tulisi olla pienempi, yleensä 1/3.
neljä. Muotin rakenne ja jalostustaso
On tunnettua, että muotin rakenteella ja prosessoinnin laadulla on tärkeä vaikutus vahamuotin kokoon ja geometriaan. Esimerkiksi onko asemointi- ja kiristysmekanismi tarkka ja luotettava, onko liikkuvien osien (kuten liikkuvien lohkojen, pulttien jne.) Sopivuusväli sopiva, onko piirtomenetelmä hyödyllinen valujen mittatarkkuuden varmistamiseksi , jne. On sanomattakin selvää, että huomattavan määrän kotimaisten investointivalukappaleiden osalta muotin suunnittelun ja valmistuksen tasoa on vielä parannettava pikaisesti.
Viisi. tiivistettynä
Edellä esitetyn analyysin perusteella ei ole vaikeaa nähdä, että investointivalujen mittatarkkuuden parantaminen on järjestelmällinen hanke, joka sisältää kaikki investointivalun tuotantoprosessin näkökohdat. Pääkohdat voidaan tiivistää seuraavasti:
1) Hallitse tiukasti muovausprosessin parametreja, erityisesti parametreja, joilla on merkittävä vaikutus valun kokoon.
2) Valitse sopiva kuorimateriaali.
3) Kerää, laske ja analysoi kutistumiseen liittyviä tietoja oikealla menetelmällä, joka vastaa tilastollisia periaatteita kutistumismäärityksen tarkkuuden parantamiseksi.
4) Tarkkaile usein mittausjärjestelmää (mukaan lukien laitteet, tarkastushenkilöstö ja tekniikka) varmistaaksesi, että toistettavuus- ja toistettavuusvirheet täyttävät määritetyt vaatimukset.
5) Parantaa jatkuvasti muotin suunnittelun ja valmistuksen tasoa.
6) Valun korjaus- ja stabilointilämpökäsittelyn kaltaiset toimenpiteet ovat edelleen välttämättömiä monissa tilanteissa
Säilytä tämän artikkelin lähde ja osoite uudelleenpainamista varten: Eri tekijät, jotka vaikuttavat sijoitusvalujen mittojen vakauteen
Minghe Die Casting Company ovat omistautuneet valmistukseen ja tarjoavat laadukkaita ja korkean suorituskyvyn valukomponentteja (metalliset painevalukappaleet sisältävät pääasiassa Ohutseinäinen valukappale,Kuuma kamari die casting,Kylmäkammion die casting), Pyöreä palvelu (painevalupalvelu,CNC-työstö,Muotin valmistus, Pintakäsittely) .Jokainen räätälöity alumiinipainevalu, magnesium- tai Zamak / sinkkipainevalu ja muut valutarvikkeet ovat tervetulleita ottamaan yhteyttä meihin.
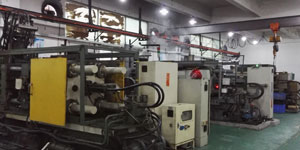
Kaikki prosessit suoritetaan ISO9001: n ja TS 16949: n valvonnassa satojen kehittyneiden painevalukoneiden, 5-akselisten koneiden ja muiden laitteiden kautta, aina blastereista Ultra Sonic -pesukoneisiin. kokeneiden insinöörien, käyttäjien ja tarkastajien tiimi asiakkaan suunnittelun toteuttamiseksi.
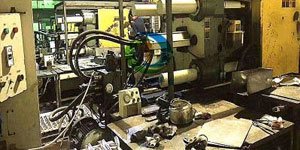
Painevalujen sopimusvalmistaja. Toiminnot sisältävät kylmäkammion alumiinipainevalukappaleet, joiden paino on 0.15 paunaa. 6 lbs., nopea vaihto ja koneistus. Lisäarvopalveluihin kuuluvat kiillotus, tärinä, purseiden poisto, puhallus, maalaus, pinnoitus, päällystys, kokoonpano ja työkalut. Materiaalit, joiden kanssa on työskennelty, sisältävät seoksia, kuten 360, 380, 383 ja 413.
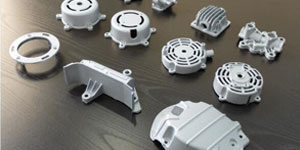
Sinkkipainevalusuunnitteluapu / samanaikaiset suunnittelupalvelut. Mukautettujen sinkkipainevalujen valmistaja. Pienikokoisia valuja, korkeapainevalukappaleita, moniliukuisia muottivaluja, tavanomaisia muottivaluja, yksikkömuotteja ja itsenäisiä muottivaluja ja ontelosuljettuja valukappaleita voidaan valmistaa. Valukappaleita voidaan valmistaa pituudeltaan ja leveydeltään jopa 24 tuumaa +/- 0.0005 tuuman toleranssilla.
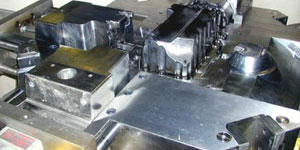
ISO 9001: 2015 -sertifioitu painevaletun magnesiumin valmistaja, ominaisuuksia ovat korkeapaineinen magneettivalumuotoinen valu jopa 200 tonnin kuumakammioon ja 3000 tonnin kylmäkammioon, työkalujen suunnittelu, kiillotus, muovaus, työstö, jauhe- ja nestemaalaus, täydellinen laadunvalvonta CMM-ominaisuuksilla , kokoonpano, pakkaus ja toimitus.
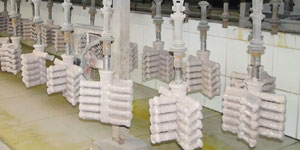
ITAF16949-sertifioitu. Lisävalupalvelu sisältää investointien valu,hiekkavalu,Painovoima valu, Lost vaahto valu,Keskipakovalu,Tyhjö valu,Pysyvä muottien valuKykyihin kuuluvat EDI, tekninen apu, vankka mallinnus ja toissijainen käsittely.
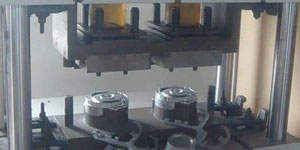
Casting Industries Osatapaustutkimukset: Autot, polkupyörät, lentokoneet, soittimet, vesijetit, optiset laitteet, anturit, mallit, elektroniset laitteet, kotelot, kellot, koneet, moottorit, huonekalut, korut, jigit, tietoliikenne, valaistus, lääkinnälliset laitteet, valokuvauslaitteet, Robotit, veistokset, äänilaitteet, urheiluvälineet, työkalut, lelut ja paljon muuta.
Mitä voimme auttaa sinua tekemään seuraavaksi?
∇ Siirry kotisivulle Die Casting Kiina
→Valuosat- Selvitä, mitä olemme tehneet.
→ Ralated-vinkkejä Die Casting palvelut
By Minghe-painevaluvalmistaja | Luokat: Hyödyllisiä artikkeleita |Materiaali Tunnisteet: Alumiinin valu, Sinkkivalu, Magnesiumvalu, Titaanivalu, Ruostumattoman teräksen valu, Messinkivalu,Pronssivalu,Suoratoista video,Yrityksen historia,Alumiinivalu | Kommentit pois päältä