Lämpökäsittelyprosessi keskustelu alumiini-magnesiumseoksesta painevalumuotista
Karkaisu- ja pintavahvistuskäsittelyprosessin käyttö on tärkeä tuotantotapa parantaa muotin suorituskykyä ja käyttöikää.Alumiini-magnesiumseoksesta valmistettujen valumuottien työolojen ja suorituskykyvaatimusten mukaan tässä artikkelissa analysoidaan muotin ominaisuuksia lämpökäsittely ja yleiset prosessit yksityiskohtaisesti, ja huomauttaa, että lämpökäsittelyprosessin eritelmien kohtuullinen muotoilu voi varmistaa muotin pinnan kovuuden, kulutuskestävyyden, ytimen lujuuden ja sitkeyden sekä estää metallin nesteen korroosiota. Muottiin tarttuminen voi vähentää tehokkaasti romun määrää ja pidentää merkittävästi muotin käyttöikää.
Alumiini-magnesiumseoksia käytetään yhä laajemmin niiden alhaisen tiheyden ja suuren lujuuden vuoksi. Niistä alumiini-magnesiumseos-painevalutekniikalla on edistyksellisenä leikkausprosessina ominaisuus korkea tuotantotehokkuus, raaka-aineiden säästäminen, tuotantokustannusten alentaminen, hyvä tuotteen suorituskyky ja korkea tarkkuus. , Käytetään pääasiassa elektroniikassa, autoissa, moottoreissa, kodinkoneissa ja muilla teollisuudenaloilla, joitain korkean suorituskyvyn, erittäin tarkkoja ja erittäin sitkeitä korkealaatuisia alumiini-magnesiumseostuotteita on sovellettu myös suuriin lentokoneisiin, laivoihin ja muille teollisuudenaloille, joilla on suhteellisen korkeat tekniset vaatimukset.
Alumiini-magnesiumseos-painevalumuotien työolot ja suorituskykyvaatimukset
Alumiini-magnesiumseos-painevalumuotti on muovausmuotti, jota käytetään alumiini-magnesiumseoksesta valmistettujen valujen valamiseen painevalukoneessa. Alumiiniseoksen sulamispiste on 600-750 ℃ ja magnesiumseoksen sulamispiste 600-700 ℃. Työskentelypinnan lämpötila voi yleensä nousta 500–600 ℃. Kaikki ontelon, tuurnan ja suuttimen pinnat altistuvat voimakkaille lämpötilan vaihteluille, ja muotin pinta on altis lämpöväsymishalkeamille. Lisäksi alumiini-magnesiumseos on helppo kiinnittää muotin pintaan painevaluprosessin aikana, mikä vaikuttaa painevalutuotannon jatkuvaan toimintaan. Nestemäisellä alumiini-magnesiumseoksella on voimakas eroosiovaikutus muotin pintaan. Siksi alumiini-magnesiumseoksesta valmistettujen muottivalujen valmistamiseksi muotimateriaalilla on oltava korkea karkaisuvakaus ja kestävyys kylmälle ja kuumuudelle noin 600 ° C: ssa, ja sillä on hyvä kestävyys korkealle lämpötilalle, korkealle paineelle, suurelle nopeudelle, ja nestemäisten alumiini-magnesiumseosten korkea eroosionkestävyys. Muotin lujuus ja sitkeys sekä samaan aikaan oikea lämpökäsittely tarvitaan muotimateriaalin potentiaalin hyödyntämiseksi ja muotin käyttöiän parantamiseksi. Tällä hetkellä yleisesti käytettyjä alumiini-magnesiumseoksesta valmistettuja valuvaluteräksiä muotinvalmistuksessa ovat: 3Cr2W8V-teräs, 4Cr5MoSiV1-teräs, 4Cr3Mo3SiV-teräs, 4Cr5MoSiV-teräs ja uudet terästyypit 4Cr5Mo2MnSiV1 ja 3Cr3Mo3VNb.
Alumiini-magnesiumseoksesta valmistetun muotin valmistusprosessi
Alumiini-magnesiumseoksesta valmistetun muottivalumuotin valmistusprosessi on: tyhjentäminen → takominen → pallomainen hehkutus → koneistus → sammutus, karkaisu → korjaus, hionta, kiillotus → nitraus (nitrocarburizing) → kokoonpano ja käyttö.
Alumiini-magnesiumseoksesta valmistetun muotin vahvistus- ja karkaisuprosessi
Alumiini-magnesiumseoksesta valmistetun valumuotin karkaisukäsittely on muuttaa teräksen rakennetta halutun rakenteen ja suorituskyvyn saavuttamiseksi. Lämpökäsittelyn tulisi perustua muotin materiaaliin, muotin muotoon, kokoon ja monimutkaisuuteen lämpökäsittelyprosessin määrittämiseksi.
3.1 Esilämpökäsittely
Painevalumuotin esilämpökäsittelyssä voidaan käyttää kolmea prosessia: jatkuva hehkutus, isoterminen hehkutus ja sammutus ja karkaisu. Tarkoituksena on saada yhtenäinen rakenne ja dispergoitu karbidi ennen viimeistä lämpökäsittelyä teräksen lujuuden ja sitkeyden parantamiseksi. Jatkuva hehkutusprosessi on suhteellisen yksinkertainen, ja voidaan myös saada parempi rakeinen perliittirakenne. Monivalmisteisille muoteille, joilla on monimutkaiset muodot ja korkeat vaatimukset, voidaan käyttää isotermistä hehkutusta ihanteellisemman rakeisen perliittirakenteen saamiseksi.
3.2 Sammutus ja esilämmitys
Valettu muottiteräs on enimmäkseen seosterästä, jonka lämmönjohtavuus on huono. Esikuumennustoimenpiteitä tehdään usein sammutuksen ja lämmityksen aikana. Esilämmityksen määrä ja lämpötila riippuvat suulateräksen koostumuksesta ja muotin muodonmuutoksen vaatimuksista. Muotteissa, joissa on matala sammutuslämpötila, yksinkertainen muoto ja alhaiset muodonmuutosvaatimukset, vaaditaan esilämmitys (800 ~ 850 ℃) sammutuksen ja lämmityksen aikana ilman halkeilua. Muottien, joissa on korkeamman lämpötilan sammutus, monimutkaiset muodot ja suuret muodonmuutosvaatimukset, tarvitaan toissijainen esilämmitys (600-650 ° C, 800-850 ° C). Tarkoituksena on vähentää lämmitysprosessin aikana syntyvää rasitusta ja samalla tehdä muotin kokonaisrakenteesta yhtenäinen.
3.3 Lämmityksen sammuttaminen
Valetun muotin sammutuslämpötila voidaan toteuttaa kunkin teräslaadun sammutuslämmitysspesifikaation mukaan. Esimerkiksi 3Cr2W8V -teräksen sammutuslämpötila on 1050 ~ 1150 ℃ ja H13 -teräksen sammutuslämpötila on 1020 ~ 1100 ℃. Kahden teräksen sammutuslämpötilan nostaminen voi lisätä painevalumuotin korkean lämpötilan lujuutta ja lämmön väsymiskestävyyttä, mutta se lisää muotin muodonmuutosta. Kuumennettaessa suolahauteessa, jotta muotin pinnalla ei tapahdu hapettavaa hiilenpoistoa, on käytettävä bariumkloridisuolahaudetta, jolla on hyvä hapetus, ja hapetus on suoritettava usein. Lämmitettäessä laatikkotyyppisessä vastusuunissa tulisi käyttää suojaavaa ilmapiiriä; tai lämmitys yleisessä laatikkotyyppisessä vastusuunissa pakkauksen jälkeen. Karbidien täydellisen liukenemisen, tasaisen austeniitin ja hyvän korkean lämpötilan suorituskyvyn varmistamiseksi painevalumuottien sammutus- ja kuumennusaikaa tulisi pidentää asianmukaisesti. Yleensä lämmityspitokerroin suolahauteessa on 0.8-1.0 min/mm.
3.4 Jäähdytä jäähdytys
Öljyn sammutusnopeus on nopea ja hyvä suorituskyky voidaan saavuttaa, mutta taipumus muodonmuutoksiin ja halkeiluihin on suuri. Yleensä käytetään öljyjäähdytteisiä painevalumuotteja, joilla on yksinkertaiset muodot ja alhaiset muodonmuutosvaatimukset; painevalumuotteille, joilla on monimutkaiset muodot ja korkeat muodonmuutosvaatimukset, on käytettävä hierarkkista sammutusta muotin muodonmuutoksen ja halkeilun estämiseksi. Sammutusjäähdytyksen tulisi olla mahdollisimman hidas vähentääkseen sammutuksen muodonmuutoksia, lämmitystä ja sammutusta tyhjiöresistanssiuunissa, jäähdytys voidaan ottaa käyttöön kaasun sammutuksessa. Lämmitys ja sammutus suolahauteessa ja luokittelukesto voidaan ottaa käyttöön jäähdytettäessä. Kun muotti sammutetaan ja jäähdytetään, se jäähdytetään yleensä 150-200 ° C: seen ja karkaistaan heti liottamisen jälkeen. Se ei saa jäähtyä huoneenlämpötilaan.
3.5 Karkaisu
Valetun muotin kovuus saavutetaan karkaisemalla, ja valumuotin ontelon kovuus vaikuttaa suoraan muotin kuumaan ja kylmään väsymisaikaan. Eri materiaalit, eri sammutuslämpötila ja karkaisulämpötila ovat myös erilaisia. Esimerkiksi 3Cr2W8V teräksen alumiini-magnesiumseoksesta valmistetun valumuotin kovuus on yleensä 42-48HRC, ja sen karkaisulämpötila valitaan yleensä välillä 560-620 ℃, mutta jos käytetään korkean lämpötilan sammutusta, karkaisulämpötila on jopa korkea 670 ℃. Kovuus 1150 ° C: n sammutuksen ja 650 ° C: n karkaisun jälkeen on 45 HRC; kun taas kovuus 1050 ° C: n sammutuksen ja 650 ° C: n karkaisun jälkeen on 35 HRC. H13-teräksen alumiini-magnesiumseoksesta valmistetun valumuotin kovuuden on oltava 44-50HRC. H13 -teräksen toissijainen kovettumispiikki näkyy, kun karkaisu tapahtuu 500 ℃: ssa, mutta piikin koko liittyy sammutuslämpötilaan. Karkaisulämpötila on yleensä 560-620 ℃. Karkaisu on suoritettava 2-3 kertaa. Ensimmäisen karkaisun lämpötila voi olla alhaisempi. Mittaa kovuuden arvo ensimmäisen karkaisun jälkeen. Jos kovuusvaatimus saavutetaan, karkaisulämpötilaa on alennettava 20 ~ 30 ℃, jotta vältetään Kovuus laskee. Jos kovuus on liian korkea, säädä karkaisulämpötila sopivasti kovuusvaatimuksen mukaan korkean kovuuden mukaan. Kolmas karkaisu on sitkeyden parantaminen, karkaisulämpötilan tulisi olla korkeampi kuin toinen
Toissijainen karkaisulämpötila on 30–50 ℃ alempi. Karkaisu- ja pitoajan tulisi olla riittävä poistamaan sammutuksen aikana syntyvä jännitys ja vähentämään muotin halkeamien muodostumista. Kunkin karkaisun pitoaika on 2 tuntia ja suurten muottien pitoaika pidennetään asianmukaisesti. Painevalumuotin korkean lämpöjännityksen ja mikrorakennerasituksen vuoksi sammutuksen jälkeen muotti yleensä karkaistaan heti 150-200 ° C: seen jäähtymisen jälkeen.
Alumiini-magnesiumseoksesta valmistetun muotin pintavahvistuskäsittely
Sammutuksen ja karkaisun jälkeen alumiini-magnesiumseoksesta valmistetun suulakkeen pinnan kovuus ei ole kovin korkea. Muotin pinnan korkean kovuuden ja kulutuskestävyyden saavuttamiseksi, kun taas ydinosa säilyttää edelleen riittävän lujuuden ja sitkeyden ja parantaa alumiini-magnesiumseoksesta valmistetun muotin tarttumista estävää suorituskykyä, pinnan nitraus tai nitraus voidaan suorittaa muottiin. Hiilihoito.
4.1 Nitridoiva hoito
Nitraus on teräspinnan lämpökäsittelyprosessi, joka lisää typpipitoisuutta pintakerroksessa. Nitrauksen tarkoituksena on vähentää muottiosien muodonmuutoksia, parantaa pinnan kovuutta, kulutuskestävyyttä, väsymislujuutta ja alumiinista ja magnesiumista valmistettuja valumuotteja, parantaa muotin korroosionkestävyyttä ilmakehää ja tulistettua höyryä vastaan, ja parantaa karkaisun ja pehmenemisen vastustuskykyä. Lohkojen herkkyys. Kiinteä, nestemäinen ja kaasun nitraus ovat tavallisia nitrausmenetelmiä. Uudet tekniikat, kuten ionin nitraus, tyhjiönitraus, elektrolyyttinen nitraus ja korkeataajuinen nitraus, voivat lyhentää suuresti nitrausjaksoa, saada korkealaatuisen nitrauskerroksen ja parantaa yritysten taloudellista tehokkuutta, joten niitä käytetään laajalti tuotannossa.
4.2 Typpikarburointi
Typpikarburointi on ammoniakkia ja alkoholinestettä (metanoli, etanoli) ja läpäiseviä väliaineita, kuten urea, formyyliliima ja trietanoliliima. Lämpöhajoamisreaktio tapahtuu tietyssä lämpötilassa, jolloin muodostuu aktiivisia typpi- ja hiiliatomeja, jotka on valettu alumiini-magnesiumseoksilla. Kun muotin pinta on imeytynyt, se diffundoituu ja tunkeutuu muotin pintakerrokseen, jolloin saadaan typpipohjainen nitrohiilikerros, jolloin muotti saa korkeamman pinnan kovuuden, väsymiskestävyyden, kulutuskestävyyden ja korroosionkestävyyden. Typpikarburointimenetelmät sisältävät neste- ja kaasumenetelmiä, ja suurin osa tuotannossa käytetyistä menetelmistä on kaasun typpikarburointi. H13-teräksestä valmistettua alumiiniseoksesta valmistettua valumuottia kuumennetaan kahdessa esilämmitysvaiheessa 550 ℃ × 40 min ja 850 ℃ × 40 min korkeassa lämpötilassa suolahauteessa, sammutetaan 1030 ℃, karkaistaan 600 ℃ ja sitten altistetaan kaasun typpikarburoivaan lämpökäsittelyyn 580 ℃. Kovuus on yli 900HV, matriisin kovuus on 46 ~ 48HRC, kulumiskestävyys, väsymiskestävyys ja korroosionkestävyys paranevat merkittävästi, eikä tartuntaa, kuorintaa, naarmuja ja korroosiota ole, mikä parantaa tehokkaasti käyttöikää hometta.
Yhteenveto
Tärkeänä käsittelylaitteena alumiini-magnesiumseoksesta valmistetut muotit vaikuttavat suoraan tuotteen laatuun ja taloudellisiin hyötyihin. Tutkimukset ja tilastot osoittavat, että väärän lämpökäsittelyprosessin aiheuttamat muotiviat aiheuttavat noin 50% kaikista vikoista. Siksi kohtuullinen valikoima lujittavia ja kovettavia käsittely- ja pinnanvahvistuskäsittelyprosesseja sekä lämpökäsittelyprosessien eritelmien tiukka valvonta ovat tärkeitä tapoja parantaa muotin suorituskykyä ja käyttöikää. Alumiini-magnesiumseoksesta valmistettujen muottivalujen valmistuksessa on tarpeen analysoida ja tutkia vian syitä muotin työolojen mukaan ja muotoilla kohtuullisesti lämpökäsittelyprosessit, jotta varmistetaan muotin pinnan kovuus, kulutuskestävyys, ydinlujuus ja sitkeys, estetään metalli nesteen korroosiota ja homeen tarttumista ja vähentävät tehokkaasti hylkäysnopeutta, parantavat merkittävästi muotin käyttöikää.
Säilytä tämän artikkelin lähde ja osoite uudelleenpainamista varten: Lämpökäsittelyprosessi keskustelu alumiini-magnesiumseoksesta painevalumuotista
Minghe Die Casting Company ovat omistautuneet valmistukseen ja tarjoavat laadukkaita ja korkean suorituskyvyn valukomponentteja (metalliset painevalukappaleet sisältävät pääasiassa Ohutseinäinen valukappale,Kuuma kamari die casting,Kylmäkammion die casting), Pyöreä palvelu (painevalupalvelu,CNC-työstö,Muotin valmistus, Pintakäsittely) .Jokainen räätälöity alumiinipainevalu, magnesium- tai Zamak / sinkkipainevalu ja muut valutarvikkeet ovat tervetulleita ottamaan yhteyttä meihin.
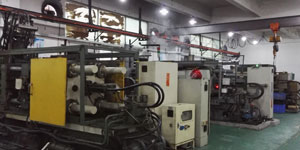
Kaikki prosessit suoritetaan ISO9001: n ja TS 16949: n valvonnassa satojen kehittyneiden painevalukoneiden, 5-akselisten koneiden ja muiden laitteiden kautta, aina blastereista Ultra Sonic -pesukoneisiin. kokeneiden insinöörien, käyttäjien ja tarkastajien tiimi asiakkaan suunnittelun toteuttamiseksi.
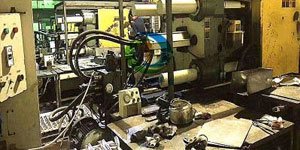
Painevalujen sopimusvalmistaja. Toiminnot sisältävät kylmäkammion alumiinipainevalukappaleet, joiden paino on 0.15 paunaa. 6 lbs., nopea vaihto ja koneistus. Lisäarvopalveluihin kuuluvat kiillotus, tärinä, purseiden poisto, puhallus, maalaus, pinnoitus, päällystys, kokoonpano ja työkalut. Materiaalit, joiden kanssa on työskennelty, sisältävät seoksia, kuten 360, 380, 383 ja 413.
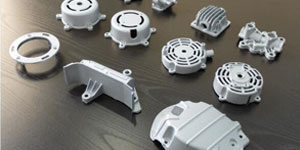
Sinkkipainevalusuunnitteluapu / samanaikaiset suunnittelupalvelut. Mukautettujen sinkkipainevalujen valmistaja. Pienikokoisia valuja, korkeapainevalukappaleita, moniliukuisia muottivaluja, tavanomaisia muottivaluja, yksikkömuotteja ja itsenäisiä muottivaluja ja ontelosuljettuja valukappaleita voidaan valmistaa. Valukappaleita voidaan valmistaa pituudeltaan ja leveydeltään jopa 24 tuumaa +/- 0.0005 tuuman toleranssilla.
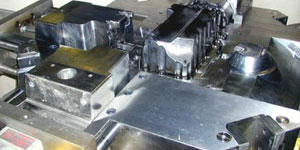
ISO 9001: 2015 -sertifioitu painevaletun magnesiumin valmistaja, ominaisuuksia ovat korkeapaineinen magneettivalumuotoinen valu jopa 200 tonnin kuumakammioon ja 3000 tonnin kylmäkammioon, työkalujen suunnittelu, kiillotus, muovaus, työstö, jauhe- ja nestemaalaus, täydellinen laadunvalvonta CMM-ominaisuuksilla , kokoonpano, pakkaus ja toimitus.
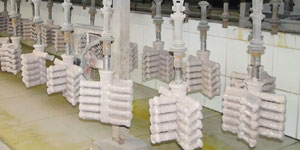
ITAF16949-sertifioitu. Lisävalupalvelu sisältää investointien valu,hiekkavalu,Painovoima valu, Lost vaahto valu,Keskipakovalu,Tyhjö valu,Pysyvä muottien valuKykyihin kuuluvat EDI, tekninen apu, vankka mallinnus ja toissijainen käsittely.
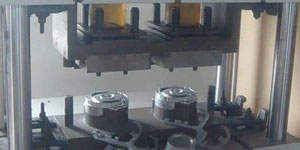
Casting Industries Osatapaustutkimukset: Autot, polkupyörät, lentokoneet, soittimet, vesijetit, optiset laitteet, anturit, mallit, elektroniset laitteet, kotelot, kellot, koneet, moottorit, huonekalut, korut, jigit, tietoliikenne, valaistus, lääkinnälliset laitteet, valokuvauslaitteet, Robotit, veistokset, äänilaitteet, urheiluvälineet, työkalut, lelut ja paljon muuta.
Mitä voimme auttaa sinua tekemään seuraavaksi?
∇ Siirry kotisivulle Die Casting Kiina
→Valuosat- Selvitä, mitä olemme tehneet.
→ Ralated-vinkkejä Die Casting palvelut
By Minghe-painevaluvalmistaja | Luokat: Hyödyllisiä artikkeleita |Materiaali Tunnisteet: Alumiinin valu, Sinkkivalu, Magnesiumvalu, Titaanivalu, Ruostumattoman teräksen valu, Messinkivalu,Pronssivalu,Suoratoista video,Yrityksen historia,Alumiinivalu | Kommentit pois päältä