Vesilasin hiekkavalun varotoimet
Mitkä tekijät vaikuttavat vesilasin "ikääntymiseen"? Kuinka poistaa vesilasin "ikääntyminen"?
Juuri valmistettu vesilasi on todellinen ratkaisu. Kuitenkin varastointiprosessin aikana vesilasin piihappo käy läpi kondensaatiopolymeroitumisen, joka vähitellen polykondensoituu todellisesta liuoksesta makromolekulaariseksi piihappoliuokseksi ja lopulta tulee piihappogeeliksi. Siksi vesilasi on itse asiassa heterogeeninen seos, joka koostuu polysilicic -haposta, jolla on erilainen polymerointiaste, johon sen moduuli, pitoisuus, lämpötila, elektrolyyttipitoisuus ja varastointiaika vaikuttavat helposti.
Varastoinnin aikana vesilasimolekyylit kondensoituvat, jolloin muodostuu geeli, ja sen sitomiskyky heikkenee vähitellen varastointiajan pidentyessä. Tätä ilmiötä kutsutaan vesilasin "ikääntymiseksi".
"Vanhenemisilmiö" voidaan selittää seuraavilla kahdella testitietojoukolla: korkea moduuli vesilasi (M = 2.89, ρ = 1.44g/cm3) 20, 60, 120, 180, 240 päivän varastoinnin jälkeen, CO2 kovettuu vesilasi puhalletaan Hiekan kuiva vetolujuus putoaa vastaavasti 9.9%, 14%, 23.5%, 36.8%ja 40%; matalan moduulin natriumsilikaattia (M = 2.44, ρ = 1.41 g/cm3) säilytetään 7, 30, 60 ja 90 päivää kuivumisen jälkeen. Vetolujuus laski 4.5%, 5%, 7.3% ja 11%.
Vesilasin varastointiajalla ei ole juurikaan vaikutusta esterikarkaistun vesilasin itsekovettuvan hiekan alkuperäiseen lujuuteen, mutta sillä on merkittävä vaikutus myöhempään lujuuteen. Mittausten mukaan se pienenee noin 60% korkean moduulin vesilasilla ja 15-20% matalan moduulin vesilasilla. . Jäännöslujuus pienenee myös säilytysajan pidentyessä.
Vesilasin varastoinnin aikana polysiliinihapon polykondensaatio ja depolymerointi etenevät samanaikaisesti, molekyylipaino on suhteeton ja lopulta monidispergoitu järjestelmä, jossa monoortosiliinihappoa ja kolloidisia hiukkasia esiintyy samanaikaisesti. Toisin sanoen vesilasin vanhenemisprosessin aikana piihapon polymeroitumisaste on suhteeton, ja mono -rikkihapon ja korkean polysiliinihapon pitoisuus kasvaa säilytysajan pidentyessä. Kondensaatiopolymeroinnin ja vesilasin depolymerointireaktion seurauksena varastoinnin aikana sidoslujuus heikkenee, eli "vanheneminen" tapahtuu.
Tärkeimmät vesilasin "vanhenemiseen" vaikuttavat tekijät ovat: varastointiaika, moduuli ja vesilasin pitoisuus. Mitä pidempi varastointiaika, sitä suurempi moduuli ja suurempi pitoisuus, sitä vakavampi "ikääntyminen".
Pitkään olemassa olevaa vesilasia voidaan muokata monin eri tavoin "ikääntymisen" poistamiseksi ja vesilasin makean veden lasin suorituskyvyn palauttamiseksi:
1. Fyysinen muutos
Vesilasin vanheneminen on spontaani prosessi, joka vapauttaa hitaasti energiaa. "Vanhennetun" vesilasin fyysinen muutos on käyttää magneettikenttää, ultraääntä, korkeataajuutta tai lämmitystä energian tuottamiseksi vesilasijärjestelmään ja edistää polysilikaattiliiman korkeaa polymeroitumista. Hiukkaset depolymerisoituvat uudelleen ja edistävät polysilicihapon molekyylipainon homogenisaatiota poistamalla siten ikääntymisilmiön, joka on fysikaalisen muuntamisen mekanismi. Esimerkiksi magneettikentällä käsittelyn jälkeen natriumsilikaattihiekan lujuus kasvaa 20-30%, lisätyn natriumsilikaatin määrä vähenee 30-40%, CO2 säästyy, kokoonpuristuvuus paranee ja on hyvä taloudellista hyötyä.
Fyysisen muokkauksen haittana on, että se ei ole kestävä ja liimauslujuus heikkenee varastoinnin jälkeen, joten se soveltuu käytettäväksi mahdollisimman pian valimon käsittelyn jälkeen. Erityisesti vesilasilla, jonka M> 2.6, piihappomolekyylien pitoisuus on suuri, ja fyysisen muuntamisen ja depolymeroinnin jälkeen se polykondensoituu suhteellisen nopeasti. On parasta käyttää sitä heti hoidon jälkeen.
2. Kemiallinen muutos
Kemiallinen modifikaatio on lisätä pieni määrä yhdisteitä vesilasiin, kaikki nämä yhdisteet sisältävät karboksyyli-, amidi-, karbonyyli-, hydroksyyli-, eetteri-, amino- ja muita polaarisia ryhmiä, jotka adsorboituvat piihappomolekyyleihin tai kolloidihiukkasiin vety sidosten tai staattisten sähköä. Pinta, muuttaa sen pintapotentiaalienergiaa ja liukenemiskykyä, parantaa polysiliinihapon vakautta estäen siten "ikääntymisen" etenemisen.
Esimerkiksi lisäämällä vesilasiin polyakryyliamidia, modifioitua tärkkelystä, polyfosfaattia jne. Voidaan saavuttaa parempia tuloksia.
Orgaanisen aineen sisällyttäminen tavalliseen vesilasiin tai jopa muunnettuun vesilasiin voi toimia monella tavalla, kuten: muuttaa vesilasin viskoosisia virtausominaisuuksia; vesilasiseosten mallinnuskyvyn parantaminen; liimauslujuuden lisääminen, jotta vesilasi lisätään kokonaan Määrä vähenee; piihappogeelin plastisuus paranee; jäännöslujuus pienenee, joten vesilasihiekka sopii paremmin valuraudalle ja ei-rautametalliseoksille.
3. Fysikaaliskemiallinen muutos
Fyysinen muokkaus soveltuu "vanhentuneelle" vesilasille, ja sitä voidaan käyttää heti muutoksen jälkeen. Kemiallinen modifiointi soveltuu makean veden lasin käsittelyyn, ja muokattu vesilasi voidaan säilyttää pitkään. Fyysisen ja kemiallisen muokkauksen yhdistelmä voi saada vesilasin muuttumaan pysyvästi. Esimerkiksi polyakryyliamidin lisääminen autoklaaviin "ikääntyvän" vesilasin muuttamiseksi on hyvä vaikutus. Niistä käytetään autoklaavin painetta ja painetta. Sekoittaminen on fysikaalinen muunnos, ja polyakryyliamidin lisääminen on kemiallinen muutos.
Kuinka estää CO2 -puhallus karkaistua natriumsilikaattihiekkamuotin (ytimen) pinnan liituutumista?
Kun natrium -silikaattihiekka on puhallettu CO2 -kovetettuna ja jätetty hetkeksi, joskus alemman muotin (ytimen) pinnalle ilmestyy huurun kaltaista ainetta, mikä vähentää vakavasti paikan pintalujuutta ja tuottaa helposti hiekkaa pesuviat kaatamisen aikana. Analyysin mukaan tämän valkoisen aineen pääkomponentti on NaHCO3, joka voi johtua liiallisesta kosteudesta tai hiilidioksidista natriumsilikaattihiekassa. Reaktio on seuraava:
- Na2CO3+H2O → NaHCO3+NaOH
- Na2O+2CO2+H2O→2NaHCO3
- NaHCO3 siirtyy helposti ulos kosteuden kanssa, jolloin muotin ja ytimen pinnalle muodostuu jauhemaista jäätä.
Ratkaisu on seuraava:
- Säädä natriumsilikaattihiekan kosteuspitoisuus liian korkeaksi (etenkin sadekaudella ja talvella).
- CO2 -puhallusaika ei saisi olla liian pitkä.
- Kovettunutta muottia ja ydintä ei saa sijoittaa pitkäksi aikaa, vaan ne on muotoiltava ja kaadettava ajoissa.
- Lisäämällä natriumsilikaattihiekkaan noin 1% (massaosa) siirappia, jonka tiheys on 1.3 g/cm3, voidaan tehokkaasti estää pinnan jauhentuminen.
Kuinka parantaa vesilasihiekkamuotin (ydin) kosteuden imeytymiskestävyyttä?
Soodaveden lasinen hiekkaydin, joka on kovetettu hiilidioksidilla tai lämmitysmenetelmillä, kootaan märään savimuottiin. Jos sitä ei kaadeta ajoissa, hiekkasydämen lujuus heikkenee jyrkästi, ei vain voi ryömiä, jopa romahtaa; sitä säilytetään kosteassa ympäristössä. Myös hiekkasydämen lujuus heikkenee merkittävästi. Taulukossa 2 esitetään hiilidioksidikarkaistun natriumveden lasihiekkasydämien lujuusarvot, kun ne asetetaan 1%: n suhteelliseen kosteuteen 2 tunniksi. Syy voimakkuuden heikkenemiseen, kun sitä säilytetään kosteassa ympäristössä, johtuu natriumvesilasin uudelleenhydraatiosta. Natriumsilikaattisidosmatriisissa olevat Na+ ja OH— absorboivat kosteutta ja syövyttävät matriisia rikkomalla lopulta pii-happisidoksen Si-O-Si, mikä johtaa natriumsilikaattihiekan sidoslujuuden merkittävään laskuun.
Toimenpiteet tämän ongelman ratkaisemiseksi ovat:
- 1. Litiumvesilasi lisätään natriumvesilasiin tai Li2CO3, CaCO3, ZnCO3 ja muut epäorgaaniset lisäaineet natriumvesilasiin, koska suhteellisen liukenemattomia karbonaatteja ja silikaatteja voi muodostua ja vapaita natriumioneja voidaan vähentää. natriumvesi -sideaineen absorptiokestävyyttä voidaan parantaa.
- 2. Lisää natriumvesilasiin pieni määrä orgaanista materiaalia tai orgaanista ainetta, jolla on pinta -aktiivinen aine. Kun sideaine on kovettunut, natriumvesilasigeelin hydrofiiliset Na+ ja OH-ionit voidaan korvata orgaanisilla hydrofobisilla ryhmillä tai yhdistettynä toisiinsa, paljastunut orgaaninen hydrofobinen emäs parantaa kosteuden imeytymistä.
- 3. Paranna vesilasin moduulia, koska korkean moduulin vesilasin kosteudenkestävyys on vahvempi kuin matalan moduulin vesilasin.
- 4. Lisää tärkkelyshydrolysaatti natriumsilikaattihiekkaan. Parempi tapa on käyttää tärkkelyshydrolysaattia natriumvesilasin muokkaamiseen.
4 Mitkä ovat CO2-puhalluskarkaistun veden lasi-alkali-fenolihartsihiekkakomposiittimenetelmän ominaisuudet?
Viime vuosina teräsvalujen laadun parantamiseksi joidenkin pienten ja keskisuurten yritysten on pikaisesti otettava käyttöön hartsihiekkaprosessi. Rajoitetun taloudellisen kapasiteetin vuoksi he eivät kuitenkaan voi ostaa hartsihiekan regenerointilaitteita, eikä vanhaa hiekkaa voida kierrättää ja käyttää uudelleen, mikä johtaa korkeisiin tuotantokustannuksiin. Jotta löydettäisiin tehokas tapa parantaa valujen laatua ilman, että kustannukset nousevat liikaa, prosessin ominaisuudet voidaan yhdistää CO2 -puhalluskarkaistua natriumsilikaattihiekkaa ja CO2 -puhalluskarkaistua alkalista fenolihartsihiekkaa yhdistettäessä ja CO2 -puhallus kovetettua natriumsilikaattia - alkalista fenolihartsia voidaan käyttää. Hartsihiekan sekoitusprosessissa käytetään emäksistä fenolihartsihiekkaa pintahiekana ja vesilasihiekkaa takahiekana ja puhalletaan hiilidioksidia kovettumiseen.
Fenolihartsi, jota käytetään CO2-emäksisessä fenolihartsihiekassa, valmistetaan fenolin ja formaldehydin polykondensaatiolla vahvan alkalisen katalyytin vaikutuksesta ja lisäämällä kytkentäainetta. Sen PH -arvo on ≥13 ja viskositeetti ≤500mPa • s. Hiekkaan lisätyn fenolihartsin määrä on 3–4% (massafraktio). Kun CO2 -virtausnopeus on 0.8 - 1.0 m3/h, paras puhallusaika on 30 ~ 60 s; jos puhallusaika on liian lyhyt, hiekkasydämen kovettumislujuus on alhainen; jos puhallusaika on liian pitkä, hiekkasydämen lujuus ei kasva ja se on hukkaan menevää kaasua.
CO2 - Alkalinen fenolihartsihiekka ei sisällä haitallisia alkuaineita, kuten N, P, S jne., Joten näiden elementtien aiheuttamat valuhäiriöt, kuten huokoset, pinnan mikrohalkeamat jne., Eliminoidaan. haitallisia kaasuja, kuten H2S ja SO2, ei vapaudu kaatamisen aikana, mikä on hyödyllistä ympäristönsuojelulle; Hyvä kokoontaitettavuus, helppo puhdistaa; korkea mittatarkkuus; korkea tuotantotehokkuus.
CO2-puhalluskarkaistu vesilasi-alkali-fenolihartsihiekkakomposiittiprosessia voidaan käyttää laajasti teräsvaluissa, rautavaluissa, kupariseoksissa ja kevytmetallivaluissa.
Yhdistelmäprosessi on yksinkertainen ja kätevä prosessi. Prosessi on seuraava: sekoita ensin hartsihiekka ja natriumsilikaattihiekka erikseen ja laita ne sitten kahteen hiekka -astiaan; lisää sitten sekoitettu hartsihiekka pintahiekana hiekkalaatikkoon ja punta, pintahiekkakerroksen paksuus on yleensä 30-50 mm; sitten lisätään vesilasihiekkaa, jotta takahiekka täyttyy ja tiivistyy; lopuksi CO2 -kaasua puhalletaan muottiin kovettumista varten.
Puhallusputken halkaisija on yleensä 25 mm ja kovettumisalue on noin 6 kertaa puhallusputken halkaisija.
Puhallusaika riippuu hiekkamuotin (ytimen) poistotulpan koosta, muodosta, kaasuvirrasta ja alueesta. Yleensä puhallusaikaa säädetään 15-40 sekunnin sisällä.
Kovan hiekkamuotin (ydin) puhalluksen jälkeen muotti voidaan ottaa. Hiekkamuotin (ydin) lujuus kasvaa nopeasti. Harjaa maali puolen tunnin kuluessa muotin ottamisesta ja sulje laatikko kaatamista varten 4 tunnin kuluttua.
Komposiittiprosessi soveltuu erityisesti teräksen valulaitoksille, joissa ei ole hartsihiekan regenerointilaitteistoa ja joiden on valmistettava korkealaatuisia valuja. Prosessi on yksinkertainen ja helppo hallita, ja valmistettujen valujen laatu vastaa muita hartsihiekkavaluja.
CO2-puhalluskarkaistu natriumsilikaattihiekka voidaan myös yhdistää CO2-puhalluskarkaistuun natriumpolyakrylaattihartsihiekkaan erilaisten korkealaatuisten valujen valmistamiseksi.
Mitkä ovat CO2-orgaanisen esterikomposiittikarkaistun natriumsilikaattihiekkaprosessin edut ja haitat?
Viime vuosina CO2-orgaaninen esterikomposiittikarkaistu natriumsilikaattihiekkaprosessi on laajentanut sovelluksiaan. Prosessi on seuraava: lisää tietty määrä orgaanista esteriä hiekan sekoittamisen aikana (yleensä puolet normaalista vaaditusta määrästä tai 4-6% vesilasin painosta); kun mallinnus on valmis, puhalla CO2 kovettumaan muotin irrotuslujuuteen (puristuskestävyys vaaditaan yleensä) lujuus on noin 0.5 MPa); purkamisen jälkeen orgaaninen esteri jatkaa kovettumistaan ja muovaushiekan lujuus kasvaa nopeammin; kun CO2 on puhallettu ja asetettu 3-6 tunniksi, hiekkamuotti voidaan yhdistää ja kaataa.
Kovettumismekanismi on:
Kun vesilasihiekka puhaltaa hiilidioksidia, kaasun paine -eron ja pitoisuuseron vaikutuksesta CO2 -kaasu yrittää virrata muovaushiekan kaikkiin suuntiin. Kun CO2 -kaasu koskettaa vesilasia, se reagoi välittömästi sen kanssa muodostaen geelin. Diffuusiovaikutuksen ansiosta reaktio tapahtuu aina ulkopuolelta sisäpuolelle, ja ulompi kerros muodostaa ensin geelikalvon, joka estää CO2 -kaasun ja vesilasin reaktion jatkumisen. Siksi lyhyessä ajassa, riippumatta siitä, mitä menetelmää käytetään CO2 -kaasun hallintaan, on mahdotonta saada se reagoimaan kaiken vesilasin kanssa. Analyysin mukaan kun muovaushiekka saavuttaa parhaan puhalluslujuuden, vesilasi reagoi CO2 -kaasun kanssa noin 2%. Tämä tarkoittaa, että vesilasi ei täysin sitoo vaikutustaan ja vähintään 65% vesilasista ei reagoi. Orgaaninen esterikovetin voi muodostaa yhtenäisen seoksen sideaineen kanssa ja voi antaa täyden välyksen sideaineen sidosvaikutukselle. Kaikki ydinhiekan osat lisäävät voimaa samalla nopeudella.
Lisääntyneen vesilasin määrän lisääminen lisää hiekkamuotin lopullista lujuutta, mutta myös sen jäännöslujuus kasvaa, mikä vaikeuttaa hiekan puhdistamista. Kun lisätty määrä vesilasia on liian pieni, lopullinen lujuus on liian pieni eikä voi täyttää käyttövaatimuksia. Todellisessa tuotannossa lisätyn vesilasin määrää säädetään yleensä noin 4%: iin.
Kun käytetään kovettamiseen pelkästään orgaanista esteriä, yleinen orgaanisen esterin määrä on 8-15% vesilasin määrästä. Komposiittikarkaisua käytettäessä arvioidaan, että noin puolet vesilasista on kovettunut hiilidioksidia puhaltaessa ja noin puolet vesilasista ei ole vielä kovettunut. Siksi on sopivampaa, että orgaanisten esterien määrä muodostaa 2–4% vesilasin määrästä.
Komposiittikarkaisumenetelmä voi antaa täyden pelin hiilidioksidikarkaisun ja orgaanisen esterikarkaisun kahdelle edulle, ja se voi täysin käyttää vesilasin sidosvaikutusta nopean kovettumisnopeuden, varhaisen muotin vapautumisen, korkean lujuuden, hyvän kokoonpuristuvuuden ja alhaisten kustannusten saavuttamiseksi. Kattava vaikutus.
CO2-orgaanisen esterikomposiittikarkaisuprosessin on kuitenkin lisättävä 0.5–1% enemmän vesilasia kuin yksinkertainen orgaaninen esterikarkaisumenetelmä, mikä lisää käytetyn vesilasihiekan regeneroinnin vaikeutta.
Miksi tahmean hiekan tuottaminen on helppoa, kun rautavalujen valmistuksessa käytetään natriumsilikaattihiekkaprosessia? Miten sen voi estää?
Kun natriumsilikaattihiekasta valmistettua hiekkamuottia (ydintä) käytetään rautavalujen kaatamiseen, syntyy usein vakavaa tahmeaa hiekkaa, mikä rajoittaa sen käyttöä valuraudan valmistuksessa.
Na2O, SiO2 natriumsilikaattihiekassa ja nestemäisen metallin tuottama rautaoksidi muodostavat heikosti sulavaa silikaattia. Kuten aiemmin mainittiin, jos tämä yhdiste sisältää enemmän sulavaa amorfista lasia, tämän lasikerroksen ja valupinnan välinen sidosvoima on hyvin pieni ja kutistumiskerroin on erilainen kuin metallin. Suuri jännitys on helppo poistaa valupinnalta ilman hiekan tarttumista. Jos valupinnalle muodostuneella yhdisteellä on suuri SiO2 -pitoisuus ja alhainen FeO-, MnO- jne. Pitoisuus, sen jähmettyneellä rakenteella on pohjimmiltaan kiteinen rakenne, joka yhdistetään tiukasti valuun, jolloin saadaan tahmeaa hiekkaa .
Kun natriumsilikaattihiekkaa käytetään rautavalujen valmistamiseen, rauta ja mangaani eivät hapetu helposti rautavalujen alhaisen kaatolämpötilan ja korkean hiilipitoisuuden vuoksi, ja tuloksena olevalla tahmealla hiekkakerroksella on kiteinen rakenne ja se on vaikeaa sopivan kerroksen muodostamiseksi rautavalujen ja tahmean hiekkakerroksen väliin. Rautaoksidikerroksen paksuus on erilainen kuin valu- ja tahmean hiekkakerroksen välinen hartsihiekka, joka voi tuottaa kirkkaan hiilikalvon hartsipyrolyysin aikana valurautavalmisteita valmistettaessa, joten tahmea hiekkakerros ei ole helppo poistaa.
Jotta voitaisiin estää soodaveden lasihiekan valmistus rautavalujen valmistuksesta, voidaan käyttää sopivia pinnoitteita. Kuten vesipohjainen maali, pinta on kuivattava maalauksen jälkeen, joten alkoholipohjainen nopeasti kuivuva maali on paras.
Yleensä rautavalut voivat myös lisätä sopivan määrän kivihiilijauhetta (kuten 3% - 6%) (massafraktio) natriumsilikaattihiekkaan, jotta hiilijauheen pyrolyysi valun ja hiekkakerroksen välillä voi tuottaa kirkas hiilikalvo. Metallit ja niiden oksidit eivät kastele sitä, joten tahmea hiekkakerros irrotetaan helposti valusta.
Onko natriumsilikaattihiekasta odotettavissa ympäristöystävällistä muovaushiekkaa ilman hiekkajätettä?
Vesilasi on väritön, hajuton ja myrkytön. Se ei aiheuta vakavia ongelmia, jos se koskettaa ihoa ja vaatteita ja huuhtelee vedellä, mutta sitä on vältettävä roiskumasta silmiin. Vesilasissa ei ole ärsyttäviä tai haitallisia kaasuja, jotka vapautuvat hiekan sekoittamisen, mallinnuksen, kovettumisen ja kaatamisen aikana, eikä siinä ole mustia ja happoja. Jos prosessi on kuitenkin väärä ja lisätään liikaa natriumsilikaattia, natriumsilikaattihiekan kokoonpuristuvuus ei ole hyvä ja pöly lentää hiekanpuhdistuksen aikana, mikä myös aiheuttaa saastumista. Samaan aikaan vanhaa hiekkaa on vaikea uudistaa, ja hiekkajätteet aiheuttavat emäksistä saastumista ympäristölle.
Jos nämä kaksi ongelmaa voidaan ratkaista, natriumsilikaattihiekasta voi tulla ympäristöystävällistä muovaushiekkaa ilman, että hiekkapäästöjä ei käytännössä ole.
Perustoimenpide näiden kahden ongelman ratkaisemiseksi on vähentää lisätyn vesilasin määrää alle 2 prosenttiin, mikä voi pohjimmiltaan ravistaa hiekan pois. Kun lisätyn vesilasin määrää pienennetään, myös vanhan hiekan jäännös Na2O vähenee. Käyttämällä suhteellisen yksinkertaista kuivaregenerointimenetelmää, on mahdollista pitää Na2O -jäännös kiertävässä hiekassa alle 0.25%. Tämä kierrätetty hiekka voi täyttää yksittäismuovaushiekan käyttövaatimukset pienille ja keskisuurille teräsvaluille. Tällä hetkellä, vaikka vanha natriumsilikaattihiekka ei käytä kalliita ja monimutkaisia märkämenetelmiä regenerointiin, vaan käytetään suhteellisen yksinkertaista ja halpaa kuivaa menetelmää, se voidaan kierrättää kokonaan, pohjimmiltaan hiekkaa ei poisteta ja suhde hiekasta rautaan Se voidaan pienentää alle 1: 1.
Kuinka regeneroida tehokkaasti natriumsilikaattihiekka?
Jos vanhan natriumsilikaattihiekan jäännös Na2O on liian korkea, sen jälkeen kun natriumsilikaatti on lisätty hiekkaan, muovaushiekalla ei ole tarpeeksi käyttöaikaa ja liika Na2O: n kertyminen heikentää kvartsihiekan tulenkestävyyttä. Siksi jäännös Na2O on poistettava mahdollisimman paljon käytetyn natriumsilikaattihiekan regeneroinnissa.
Säilytä tämän artikkelin lähde ja osoite uudelleenpainamista varten: Vesilasin hiekkavalun varotoimet
Minghe Die Casting Company ovat omistautuneet valmistukseen ja tarjoavat laadukkaita ja korkean suorituskyvyn valukomponentteja (metalliset painevalukappaleet sisältävät pääasiassa Ohutseinäinen valukappale,Kuuma kamari die casting,Kylmäkammion die casting), Pyöreä palvelu (painevalupalvelu,CNC-työstö,Muotin valmistus, Pintakäsittely) .Jokainen räätälöity alumiinipainevalu, magnesium- tai Zamak / sinkkipainevalu ja muut valutarvikkeet ovat tervetulleita ottamaan yhteyttä meihin.
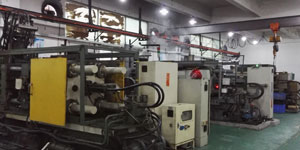
Kaikki prosessit suoritetaan ISO9001: n ja TS 16949: n valvonnassa satojen kehittyneiden painevalukoneiden, 5-akselisten koneiden ja muiden laitteiden kautta, aina blastereista Ultra Sonic -pesukoneisiin. kokeneiden insinöörien, käyttäjien ja tarkastajien tiimi asiakkaan suunnittelun toteuttamiseksi.
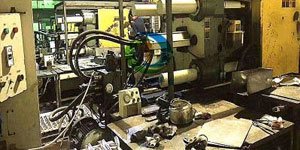
Painevalujen sopimusvalmistaja. Toiminnot sisältävät kylmäkammion alumiinipainevalukappaleet, joiden paino on 0.15 paunaa. 6 lbs., nopea vaihto ja koneistus. Lisäarvopalveluihin kuuluvat kiillotus, tärinä, purseiden poisto, puhallus, maalaus, pinnoitus, päällystys, kokoonpano ja työkalut. Materiaalit, joiden kanssa on työskennelty, sisältävät seoksia, kuten 360, 380, 383 ja 413.
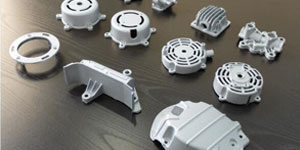
Sinkkipainevalusuunnitteluapu / samanaikaiset suunnittelupalvelut. Mukautettujen sinkkipainevalujen valmistaja. Pienikokoisia valuja, korkeapainevalukappaleita, moniliukuisia muottivaluja, tavanomaisia muottivaluja, yksikkömuotteja ja itsenäisiä muottivaluja ja ontelosuljettuja valukappaleita voidaan valmistaa. Valukappaleita voidaan valmistaa pituudeltaan ja leveydeltään jopa 24 tuumaa +/- 0.0005 tuuman toleranssilla.
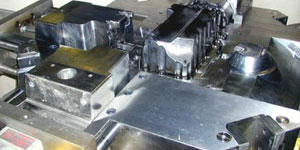
ISO 9001: 2015 -sertifioitu painevaletun magnesiumin valmistaja, ominaisuuksia ovat korkeapaineinen magneettivalumuotoinen valu jopa 200 tonnin kuumakammioon ja 3000 tonnin kylmäkammioon, työkalujen suunnittelu, kiillotus, muovaus, työstö, jauhe- ja nestemaalaus, täydellinen laadunvalvonta CMM-ominaisuuksilla , kokoonpano, pakkaus ja toimitus.
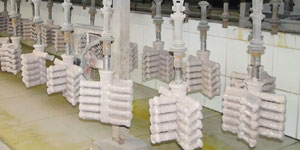
ITAF16949-sertifioitu. Lisävalupalvelu sisältää investointien valu,hiekkavalu,Painovoima valu, Lost vaahto valu,Keskipakovalu,Tyhjö valu,Pysyvä muottien valuKykyihin kuuluvat EDI, tekninen apu, vankka mallinnus ja toissijainen käsittely.
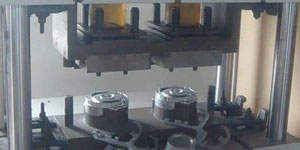
Casting Industries Osatapaustutkimukset: Autot, polkupyörät, lentokoneet, soittimet, vesijetit, optiset laitteet, anturit, mallit, elektroniset laitteet, kotelot, kellot, koneet, moottorit, huonekalut, korut, jigit, tietoliikenne, valaistus, lääkinnälliset laitteet, valokuvauslaitteet, Robotit, veistokset, äänilaitteet, urheiluvälineet, työkalut, lelut ja paljon muuta.
Mitä voimme auttaa sinua tekemään seuraavaksi?
∇ Siirry kotisivulle Die Casting Kiina
→Valuosat- Selvitä, mitä olemme tehneet.
→ Ralated-vinkkejä Die Casting palvelut
By Minghe-painevaluvalmistaja | Luokat: Hyödyllisiä artikkeleita |Materiaali Tunnisteet: Alumiinin valu, Sinkkivalu, Magnesiumvalu, Titaanivalu, Ruostumattoman teräksen valu, Messinkivalu,Pronssivalu,Suoratoista video,Yrityksen historia,Alumiinivalu | Kommentit pois päältä