Syöttölangan menetelmä Pallografiittivaluraudan käsittelyprosessi
Todellisen tuotannon avulla pallografiittivaluraudan valmistuksessa käytetään lävistysmenetelmää ja syöttömenetelmää, ja näiden kahden prosessin ominaisuudet analysoidaan. Vertailun kautta syöttömenetelmällä valmistettujen valujen kokonaisvaltainen suorituskyky on vakaampi kuin lävistysmenetelmä; ja syöttöprosessi on pallomainen. Voit jakaa joitain kokemuksia siitä.
1. Yleiskatsaus
Kuten me kaikki tiedämme, akseli on tärkeä ajoneuvon kantava osa, ja se liittyy suoraan ajoneuvon turvallisuuteen. Akselipesä on yksi akselin keskeisistä osista. Akselipesän materiaalin suorituskyky määrittää suoraan ajoneuvon kantavuuden. Tällä hetkellä raskaan kuorma -auton akselipesät on yleensä jaettu kahteen luokkaan: leimatut ja hitsatut akselipesät ja valetut akselipesät, ja valetut akselipesät voidaan jakaa teräsvaluakselipesiin ja valurauta -akselipesiin.
Valetun akselin kotelo on aina ollut raskaan kuorma-auton akselipesän pääasennossa suuren kantavuuden ja alhaisten tuotantokustannusten vuoksi. Akselipesän ankaran työympäristön ja pitkäaikaisen työn dynaamisen kuormituksen vuoksi tämä edellyttää korkeita vaatimuksia akselipesän materiaaliominaisuuksille. Vahvuuden varmistamiseksi sen on myös saatava suurempi plastisuus ja sitkeys sopeutuakseen akselipesään. Työn ominaisuudet.
Tiedämme, että nodulaarisen valuraudan osalta pallomainen prosessi on keskeinen linkki nodulaarisen valuraudan valmistuksessa, ja pallomaisen käsittelyn laatu vaikuttaa suoraan nodulaarisen valuraudan laatuun. Alussa käyttämämme sferoidisointiprosessi oli rush-in-menetelmän sferoidiprosessi. Vaikka tämä menetelmä on yksinkertainen ja helppokäyttöinen, sillä on monia puutteita, kuten: alhainen seoksen saanto; suuri savu ja huono työympäristö; reaktio Silloin tuotetun kuonan määrä on suuri; Ulkoiset tekijät vaikuttavat helposti hoitovaikutukseen, mikä johtaa valukappaleiden laadun vaihteluihin ja usein epäpätevään pallomaisuuteen. Nämä laadun vaihtelut vaikuttavat akselipesän suorituskykyyn ja jopa ajoneuvon turvallisuuteen.
Langansyöttömenetelmää, pallomaista käsittelyprosessia sovellettiin valuraudan valmistukseen. Se alkoi 1980 -luvulla ulkomailla. Vaikka nodulaarisen valuraudan kotimainen tuotanto alkoi soveltaa tätä tekniikkaa myöhään, tekniikka on suosittu ja käytetty nopeasti maassa, ja se on hyödyllinen nodulaarisen grafiitin tuotannon parantamisessa. Valuraudan laadun vakausvaikutus on ilmeinen.
2. Syöttölangan pallomainen prosessi
Langansyötön sferoidiprosessin perusperiaate on kääriä tietty koostumus jauhemaista pallomaista ainetta ja ymppäysainetta teräskuoren läpi ja lähettää se pallomaiseen käsittelypakettiin tietyllä nopeudella laitteen läpi siten, että kehän alareunassa oleva kehä paketti räjähtää. Sferoidisen inokulaatiokäsittelyn tarkoituksen saavuttamiseksi.
Tällä hetkellä hyväksymme langansyöttöpallon prosessi: säädä kemiallinen koostumus prosessivaatimuksiin, lämmitä 1510-1520 ℃ ja anna seistä paikallaan, napautuslämpötila on 1480 ~ 1500 ℃, raudan ulostulo on 2 t ja pallomaisen käsittelyn lämpötila on 1420 ~ 1450 ℃. Kaatolämpötila on 1370 ~ 1380 ℃. Rokotusnopeus virtauksen kanssa on 0.1%.
Pallonsiirtolinjan pituus on 39-46 m, säädettynä alkuperäisen sulan raudan rikkipitoisuuden mukaan. Mitä suurempi rikkipitoisuus, sitä pidempi pallomainen linja on lisättävä ja päinvastoin. Rokotuslinjan pituus on 32 m.
3. Syöttölangan pallomainen prosessi parantaa valujen laatua
Yli vuoden tuotannon jälkeen akselipesien laatu on parantunut merkittävästi aiempaan verrattuna. Erityisesti koostumuksen, metallografian ja mekaanisten ominaisuuksien vakaus on parantunut huomattavasti.
Metallografisen rakenteen vertailu Valitse kiillotettavaksi valun sama sijainti ja tarkkaile metallografista rakennetta. Otettu metallografinen kuva on esitetty kuvassa 2. Rei'itysmenetelmään verrattuna syöttömenetelmän tuottaman valun grafiittipallot ovat ohuempia ja pyöreämpiä.
4. Edut syöttölangan sferoidiprosessista
Todellisen tuotannon vertailumme mukaan langansyöttölaitteella on monia etuja verrattuna lävistysmenetelmän pallomaiseen prosessiin.
- Paikan päällä olevan tuotantoympäristön parantaminen. Kun pallomainen aine reagoi sulan raudan kanssa, syntyy suuri määrä savua ja voimakasta valoa, mikä pahentaa työympäristöä; kun langansyöttömenetelmää käytetään pallonsäteilyyn, käsittelyasema Sferoidipussin peittämiseksi on kansi ja kansi on kytketty käsittelyaseman pölynpoistojärjestelmään, joten savua käsitellään pölynpoistojärjestelmän sijasta vapautetaan suoraan työpajaan.
- Lisätyn seoksen määrä vähenee ja tuotantokustannukset pienenevät. Laskennan jälkeen 1t sulan raudan syöttömenetelmän käsittely voi säästää noin 78 yuania raaka -ainekustannuksissa kuin impulssimenetelmä. Tehtaamme vuotuisen tuotantokapasiteetin mukaan 10,000 780,000 tonnia pallografiittivalurauta -akselipesää, vuotuinen säästö on Kustannukset ovat XNUMX XNUMX yuania ja hyödyt ovat huomattavia.
- Toteuta työn automatisointi ja vähennä työntekijöiden työvoimavaltaa. Sferoidiprosessia suoritettaessa työntekijöiden alustavat valmistelut ovat hankalia, mukaan lukien pallomaisen aineen ja ymppäysaineen punnitseminen, pallomaisen aineen ja siirrostusaineen lisääminen pussiin sekä tiivistäminen ja peittäminen. langansyöttömenetelmän pallomaisten ja inokuloivien linjojen lisäys lisätään automaattisesti kytkentäkaapin kautta, mikä vähentää paljon työtä.
- Spheroidisoinnin laatu on vakaa ja sferoidiefekti on parempi. Tilastojen mukaan langansyöttöpalloiluprosessin käytön jälkeen vuonna 2013 sferoidisoinnin läpäisyaste on yli 99.5 %, kun taas sferoidiprosessin läpäisyaste on vain 95 %.
5. Kuinka syöttölangan sferoidaation prosessiparametrit valitaan oikein
Varsinaisessa tuotannossa langansyöttöprosessin parametrien oikea valinta vaatii tietyn määrän testejä sen varmistamiseksi. Olemme tehneet monia prosessisäätöjä testin järjestämisen alusta viralliseen massatuotantoon. Seuraavat jakavat kokemuksemme kollegoiden kanssa.
Jos haluat valita syöttölangan sferoidisaation prosessiparametrit oikein, sinun on kiinnitettävä huomiota seuraaviin seikkoihin:
- (1) Ydinlangan valinta Jotkut ulkomaiset kokemukset eivät suosittele korkean magneettisen langan käyttöä. Mg -pitoisuus on liian korkea, pallomaisuusreaktio on voimakas, Mg palaa paljon ja kuonan määrä on suuri. Yleensä on suositeltavaa valita noin 30%: n Mg-pitoisuus ja käyttää Ba: ta sisältävää ymppäyslankaa, joka voi tehokkaasti estää rokottamisen vähenemisen. Yrityksemme käyttämän ydinlangan pääparametrit ovat: ulomman teräsvaipan paksuus on 0.4 mm ja ydinlangan halkaisija on 13 mm. Tarkista ennen käyttöä, että ydinlangan ulkonäkö on pyöreä ja ettei siinä ole halkeamia, jauhevuotoja jne. Todellisessa tuotannossa on tarpeen säätää käsittelylämpötilan ja sulan raudan korkeuden mukaan. Yleensä mitä korkeampi käsittelylämpötila, sitä korkeampi sulan raudan korkeus ja sitä nopeampi langansyöttönopeus. Lisäksi. Joissakin materiaaleissa on myös otettu käyttöön kätevä ja toteuttamiskelpoinen menetelmä optimaalisen langansyöttönopeuden mittaamiseksi: mittaa ensin sulan raudan korkeus käsittelypussissa ja syötä sitten lankakonetta manuaalisesti niin, että ydinlanka koskettaa vain nesteen pintaa. Tyhjennä laskuri, Manuaalinen langansyöttökone suorittaa langansyötön. Kun kuulet puomin vastausäänen, tarkista syöttöpituus välittömästi. Jos tämä pituus on pohjimmiltaan sama kuin sulan raudan korkeus, nopeuden tulisi olla sopiva. Tarkistuksen jälkeen valitsimme syöttönopeuden 30 m/min.
- Langansyöttömäärän valinta Sopiva langansyöttömäärä on syöttää vähimmäissydäminen lanka oletuksella varmistaa pallomainen vaikutus. Langansyötön määrä on määritettävä sulan raudan käsittelytilavuuden, prosessilämpötilan ja sulan raudan rikkipitoisuuden mukaan. Alkuperäisen sulan raudan rikkipitoisuuden ja tuoteprosessivaatimusten mukaan yhdistettynä kokeelliseen todentamiseen, jäännösmagnesiumpitoisuuden varmistamiseksi, pallomaisen siiman pituus on 39-46 m ja ympäryslinjan pituus 32 m.
- Käsittelylämpötilan valinta Käsittelylämpötilaa on alennettava niin paljon kuin mahdollista kaatolämpötilan varmistamiseksi. Mitä alhaisempi käsittelylämpötila, sitä korkeampi magnesiumin imeytymisnopeus ja sitä pienempi langan kulutus. Todellisen tuotantotestauksen mukaan aika pallomaisen käsittelyn alusta kaatamisen alkuun on 4-5 minuuttia, jonka aikana lämpötilan lasku on 40-50 ° C ja pallomaisen reaktion kesto 80-90 sekuntia. Koska pallomaisuusprosessi on käännettävä, asetamme käsittelylämpötilaksi 1410 1450 5 ℃, yläraja otetaan, kun huonelämpötila on alle 25 ℃ ja alaraja, kun huonelämpötila on yli XNUMX ℃.
- Jäännöksen magnesiumpitoisuuden valinta sulassa raudassa käsittelyn jälkeen. Jäännösmagnesiumpitoisuus on varattava tietylle määrälle magnesiumia valun ominaisuuksien mukaan. Aluksi hallitsimme jäännösmagnesiumpitoisuuden 0.03%: sta 0.06%: iin, mutta varsinaisen tuotannon todentamisen jälkeen on sopivampaa hallita jäännösmagnesiumpitoisuus 0.05% - 0.06%: iin, koska havaitsimme, että kun magnesiumin jäännös on alle 0.04%, sen grafiitti Pallon pyöreys on hieman huonompi. Kun se on yli 0.07%, sementti on altis esiintymään ja sulan raudan kutistumis taipumus kasvaa.
- Langan tukkeutumisen ongelman ratkaiseminen käytön aikana Langan tukosilmiö esiintyy ydinlangan kuljetusprosessin aikana, jolloin koko sulan raudan pakkaus romutetaan. Tätä varten olemme toteuttaneet seuraavat toimenpiteet: yksi on asennettu teräsrengas ydinlankakelan yläpuolelle, kuten kuvassa 5 esitetään, mikä voi vähentää ydinlangan taipumista ja tehdä siitä sujuvasti ohjausmekanismiin; toinen on kahden kelan yhdistäminen Hitsauksen jälkeen kiillota suuret kuoppia hitsauksen jälkeen, jotta lanka ei tukkeudu kuljetusprosessin aikana; kolmanneksi, vältä alle 1 m: n mutkia mutkissa kuljetusputkistossa tai ydinlangan reitillä estääksesi ydinlangan kuljetuksen Jauhevuoto tai tukos prosessin aikana
6-päätelmä
- Syöttölankamenetelmän pallomaisella prosessilla on alhainen seoksen lisäysmäärä, korkea Mg -imeytymisnopeus ja se voi tehokkaasti vähentää savua ja voimakasta valosaastetta työpajassa, mikä luo hyviä taloudellisia ja ympäristöhyötyjä valimoyrityksille.
- Langansyöttömenetelmän sferoidiprosessi voi tehokkaasti vähentää pallomaisuuden epäonnistumisastetta, parantaa nodulaarisen valuraudan laatua, parantaa sen kattavia mekaanisia ominaisuuksia ja parantaa yrityksen markkinoiden kilpailukykyä.
- Jokaisen valimon on valittava sopivat prosessiparametrit lankapalloa varten omien tuotanto -olosuhteidensa ja tuoteprosessivaatimustensa mukaisesti yhdistettynä vertaistukien tuotantokokemukseen.
Syöttölinjan pallomainen prosessi voi parantaa merkittävästi nodulaarisen valuraudan laadun vakautta, vähentää tuotantokustannuksia, parantaa tuotantoympäristöä ja vähentää työntekijöiden työvoimakkuutta. Tämä on pallomaisen prosessin viimeaikainen kehityssuunta.
Säilytä tämän artikkelin lähde ja osoite uudelleenpainamista varten: Feeding Wire Method Pallografiittivalurauta käsittelyprosessi
Minghe Die Casting Company ovat omistautuneet valmistukseen ja tarjoavat laadukkaita ja korkean suorituskyvyn valukomponentteja (metalliset painevalukappaleet sisältävät pääasiassa Ohutseinäinen valukappale,Kuuma kamari die casting,Kylmäkammion die casting), Pyöreä palvelu (painevalupalvelu,CNC-työstö,Muotin valmistus, Pintakäsittely) .Jokainen räätälöity alumiinipainevalu, magnesium- tai Zamak / sinkkipainevalu ja muut valutarvikkeet ovat tervetulleita ottamaan yhteyttä meihin.
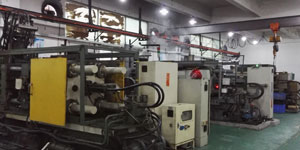
Kaikki prosessit suoritetaan ISO9001: n ja TS 16949: n valvonnassa satojen kehittyneiden painevalukoneiden, 5-akselisten koneiden ja muiden laitteiden kautta, aina blastereista Ultra Sonic -pesukoneisiin. kokeneiden insinöörien, käyttäjien ja tarkastajien tiimi asiakkaan suunnittelun toteuttamiseksi.
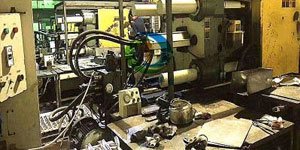
Painevalujen sopimusvalmistaja. Toiminnot sisältävät kylmäkammion alumiinipainevalukappaleet, joiden paino on 0.15 paunaa. 6 lbs., nopea vaihto ja koneistus. Lisäarvopalveluihin kuuluvat kiillotus, tärinä, purseiden poisto, puhallus, maalaus, pinnoitus, päällystys, kokoonpano ja työkalut. Materiaalit, joiden kanssa on työskennelty, sisältävät seoksia, kuten 360, 380, 383 ja 413.
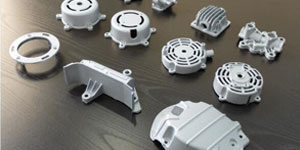
Sinkkipainevalusuunnitteluapu / samanaikaiset suunnittelupalvelut. Mukautettujen sinkkipainevalujen valmistaja. Pienikokoisia valuja, korkeapainevalukappaleita, moniliukuisia muottivaluja, tavanomaisia muottivaluja, yksikkömuotteja ja itsenäisiä muottivaluja ja ontelosuljettuja valukappaleita voidaan valmistaa. Valukappaleita voidaan valmistaa pituudeltaan ja leveydeltään jopa 24 tuumaa +/- 0.0005 tuuman toleranssilla.
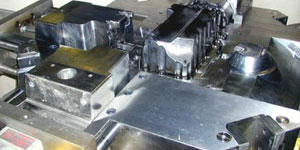
ISO 9001: 2015 -sertifioitu painevaletun magnesiumin valmistaja, ominaisuuksia ovat korkeapaineinen magneettivalumuotoinen valu jopa 200 tonnin kuumakammioon ja 3000 tonnin kylmäkammioon, työkalujen suunnittelu, kiillotus, muovaus, työstö, jauhe- ja nestemaalaus, täydellinen laadunvalvonta CMM-ominaisuuksilla , kokoonpano, pakkaus ja toimitus.
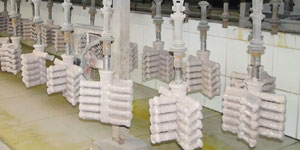
ITAF16949-sertifioitu. Lisävalupalvelu sisältää investointien valu,hiekkavalu,Painovoima valu, Lost vaahto valu,Keskipakovalu,Tyhjö valu,Pysyvä muottien valuKykyihin kuuluvat EDI, tekninen apu, vankka mallinnus ja toissijainen käsittely.
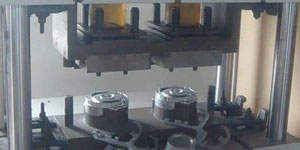
Casting Industries Osatapaustutkimukset: Autot, polkupyörät, lentokoneet, soittimet, vesijetit, optiset laitteet, anturit, mallit, elektroniset laitteet, kotelot, kellot, koneet, moottorit, huonekalut, korut, jigit, tietoliikenne, valaistus, lääkinnälliset laitteet, valokuvauslaitteet, Robotit, veistokset, äänilaitteet, urheiluvälineet, työkalut, lelut ja paljon muuta.
Mitä voimme auttaa sinua tekemään seuraavaksi?
∇ Siirry kotisivulle Die Casting Kiina
→Valuosat- Selvitä, mitä olemme tehneet.
→ Ralated-vinkkejä Die Casting palvelut
By Minghe-painevaluvalmistaja | Luokat: Hyödyllisiä artikkeleita |Materiaali Tunnisteet: Alumiinin valu, Sinkkivalu, Magnesiumvalu, Titaanivalu, Ruostumattoman teräksen valu, Messinkivalu,Pronssivalu,Suoratoista video,Yrityksen historia,Alumiinivalu | Kommentit pois päältä