Vermikulaarisen raudan tuotannon prosessinohjaus
Harmaaseen rautaan verrattuna vermikulaarisen raudan vetolujuus kasvaa vähintään 70%, elastisuusmoduuli kasvaa 35%ja väsymislujuus lähes kaksinkertaistuu. Verrattuna alumiiniseokseen vermikulaarisen raudan lujuus ja jäykkyys ovat kaksi kertaa suuremmat ja väsymislujuus kaksi kertaa suurempi. Nämä vermikulaarisen raudan ominaisuudet tarjoavat moottorille mahdollisuuden parantaa teho/paino -suhdetta ja lisätä sylinterin painetta. Lisääntyvä sylinteripaine on avain seuraavan sukupolven suoraruiskutusdieselin optimaaliseen suorituskykyyn. Vermikulaarisen raudan laajan käytön vastaamiseksi valimoteollisuus valmistelee parhaillaan aktiivisesti, investoi voimakkaasti ja rakentaa uusia prosesseja, jotta vermikulaarisen raudan tuotanto olisi vakaa ja luotettava.
Vermikulaaristen rautamoottoreiden prototyypistä massatuotantoon ratkaiseva tekijä on laaturiski. Korkealaatuisen vermikulaarisen raudan vakaa vyöhyke on hyvin pieni, vain 0.008% magnesiumpitoisuutta. Pieni määrä, kuten 0.001%: n menetys magnesiumista, tuottaa hiutalegrafiittia, mikä aiheuttaa mekaanisten ominaisuuksien heikkenemisen 25% - 40%. Tässä artikkelissa kuvataan prosessinhallintajärjestelmä, joka perustuu lämpöanalyysimenetelmiin. Järjestelmä mittaa magnesiumin menetystä ja säätää sulan raudan tilaa verkossa estääkseen hiutalegrafiitin muodostumisen. Tämä online -mittaus- ja säätömenetelmä vähentää haihtuvuutta vermikulaarisen raudan valmistusprosessissa alimpaan pisteeseen ja eliminoi pohjimmiltaan vermikulaarisen raudan tuotannon aiheuttaman laaturiskin.
Korkean hevosvoiman, suuren vääntömomentin, alhaisten pakokaasupäästöjen ja pienemmän polttoaineenkulutuksen kysyntä kasvaa edelleen. Tämä pakottaa suuritehoisten dieselmoottoreiden suunnittelijat lisäämään sytytyksen huippupainetta, mikä lisää merkittävästi moottorin lämpökuormitusta ja mekaanista kuormitusta. Lämpökuorma ja mekaaninen kuormitus kasvavat samanaikaisesti, joten tällä hetkellä käytetyt tavanomaiset valurauta- ja seosteräsvalurautamoottorit (CrMo) ovat saavuttaneet tai ylittäneet käytön ylärajan. Moottorivalmistajat tarvitsevat materiaaleja, joilla on suurempi lujuus ja parempi lämmönkestävyys.
Vermikulaarisesta raudasta on nopeasti tullut ihmisten valinta. Se parantaa merkittävästi uuden sukupolven kuorma -autojen sylinterilohkon, sylinterinkannen ja sylinterivuorauksen luotettavuutta. Jotta eri ominaisuuksien (kuten valuominaisuuksien, koneistusominaisuuksien, lämmönjohtavuuden ja mekaanisten ominaisuuksien) paras yhdistelmä saavutettaisiin, nämä osat on valmistettava pallomaisella nopeudella 0-20% (hiipumisaste 80-100%) ) Valmistettu vermikulaarisesta raudasta. Jos pallomaisuusaste ylittää 20%, se aiheuttaa useita epäedullisia tekijöitä. Esimerkiksi kutistumismäärä on liian suuri, ja monimutkaiset osat, kuten sylinterinkannet, ovat erityisen alttiita kutistumiselle. Toinen esimerkki on työkalun käyttöiän lyheneminen liiallisesta kulumisesta koneistuksen aikana. Myös lämmönjohtavuus heikkenee merkittävästi aiheuttaen lämpörasitusta ja niin edelleen. Vermikulaarisen raudan toisessa päässä hiutalegrafiitti aiheuttaa lineaarisen heikkenemisen mekaanisissa ominaisuuksissa, jolloin moottori ei pysty täyttämään uusia vaatimuksia. Yhteenvetona voidaan todeta, että uuden sukupolven kuorma-automoottoreiden tarpeiden tyydyttämiseksi korkean lujuuden omaavan raudan pallomaisuuden on oltava 0%-20% (eli hiipumisaste on yli 80% ilman hiutaleita).
Käytetäänkö tuotantoprosessin valvontaa vai ei, riippuu tuotteen vuosituotannosta, tuotteen monimutkaisuudesta ja metallografisen rakenteen sallituista muutosalueista. Kuten kuviossa 1 esitetään, suhteellisen yksinkertaisia, pienitilavuisia osia, kuten harkon muotteja, voidaan yleensä valmistaa tavanomaisilla valumenetelmillä. Prosessin hallintaa ei yleensä tarvita, eikä se ole taloudellisesti kustannustehokasta. Kun komponenttien, kuten pakoputkien, kampiakselien ja kiinnikkeiden, vuosituotanto kasvaa, prosessinhallinnan käyttöönotto olisi järkevää. Vaikka tämäntyyppisellä tuotteella on suuri vuotuinen tuotanto, valun vuotuinen tonnimäärä ei ole suuri. Metallografisen rakenteen vaatimukset eivät ole kovin tiukat, joten pallomaisuusaste voi olla jopa 50%. Lisäksi tällaisten osien pienen työstön vuoksi tuotannossa lisättävän titaanin lisäyksen voidaan sallia laajentaa hallittavaa aluetta. Tämän tyyppisille tuotteille tavanomaiset valumenetelmät ja tiukka koulutus ovat yleensä päteviä vermikulaarisen raudan valmistuksessa. Mutta laadunvalvonnan näkökulmasta prosessinhallinnan pitäisi olla turvallisempaa. Samoin prosessinohjaus takaa myös suurten merimoottorilohkojen ja sylinterinkantojen valmistuksen. Vaikka suuri koko ja pieni tuotantomäärä edistävät tuotteiden valmistusta, standardin ylittävien tuotteiden aiheuttamat taloudelliset tappiot riittävät lisäämään joukon prosessinohjausjärjestelmiä.
Tuotteita, jotka tarvitsevat eniten prosessinohjausta, ovat autojen moottorin sylinterilohot, sylinterinkannet ja jarrulevyt, joiden vuosituotanto on suuri, monimutkaisuus ja tiukat tekniset vaatimukset. Näiden tuotteiden vuotuinen tuotantomäärä ja tonnimäärä ovat erittäin suuret. Ne ovat kooltaan monimutkaisia ja vaativat metallografista rakennetta, ja niillä on taipumus tuottaa kutistumisonteloita. Näillä tuotteilla ei saa olla laaturiskejä, muuten menetys on erittäin vakava.
Moottorilohkon, sylinterinkannen ja sylinteripesän suorituskykyä koskevat tiukat vaatimukset ovat luoneet perustan tuotespesifikaatioiden valmistamiselle. Jotta saavutettaisiin paras mahdollinen valettavuuden, työstettävyyden ja mekaanisten ominaisuuksien suorituskyky, pallostuksen nopeuden tulisi olla 0-20% komponentin kaikissa keskeisissä osissa. Vielä tärkeämpää on, että hiutalegrafiittia on ehdottomasti vältettävä paikallisen heikkouden aiheuttamien osien vaurioitumisen estämiseksi. Hyvän mekaanisen additiivisuuden saavuttamiseksi vapaat karbidit on vähennettävä minimiin. Siksi titaania ei saa koskaan lisätä. Lopuksi tuotannon kannalta valimo tarvitsee vakaan ja luotettavan prosessin, jolla varmistetaan metallografisen rakenteen aiheuttama pienin romun määrä. Autoteollisuuden valmistajat vaativat laadunvarmistusta ja 100% valujen on täytettävä metallografiset vaatimukset. Laajamittainen ja luotettava sylinterilohkojen, sylinterinkansien ja sylinteripesien tuotanto vaatii tarkan analyysin ja sulan raudan online-säätämisen prosessin vaihtelujen poistamiseksi ennen kaatamista.
Vermicular raudan vakautta
Syy siihen, miksi tiivistettyä rautaa ei käytetä suuria määriä monimutkaisten osien (kuten moottorilohkojen) valmistukseen, on se, että tiivistetyn raudan vakaa pinta -ala on liian pieni varmistamaan, ettei tuotannossa ole riskiä. Yleisesti ottaen tämä vakaa vyöhyke ulottuu vain 0.008% magnesiumin alueelle, kuten kuviossa 2 on esitetty. Korin koko ja sijainti vakiovyöhykkeellä vaihtelevat tuotteen mukaan. Itse asiassa käytettävissä oleva magnesiumalue on tätä pienempi. Koska aktiivinen magnesium palaa 5 minuutin välein 0.001%. Sulan raudan alkuvuotopisteen on oltava riittävän kaukana tiivistetyn raudan terävästä kääntymispisteestä harmaaseen rautaan, jotta varmistetaan, ettei lopulliseen valettuun osaan tule hiutalegrafiittia. Kun magnesiumia lisätään sulaan rautaan, hiutalegrafiitti ilmestyy noin 15 minuutin kuluttua.
Lähtöpiste ei saa olla liian lähellä vakaan alustan oikeaa puolta (korkea magnesiumpitoisuus), muuten se aiheuttaa suuren määrän pallomaista grafiittia ohuempaan ja nopeasti jäähdyttävään osaan.
Pienen käytettävissä olevan lava -alueen lisäksi lava -alue liikkuu aina. Jos aktiivisen hapen ja rikin pitoisuus on korkea, ne kuluttavat enemmän aktiivista magnesiumia ja koko alusta siirtyy oikealle (korkea magnesiumpitoisuus). Päinvastoin, jos aktiivisen hapen ja rikin pitoisuus on alhainen, taso siirtyy vasemmalle (alhainen magnesiumpitoisuus). Muutokset raaka -aineiden koostumuksessa, puhtaudessa, hapettumisasteessa ja kosteudessa jne. Tekevät ihmisten mahdottomaksi hallita vermikulaarista rautaa kiinteällä kemiallisen koostumuksen alueella.
Vaikka muuntaminen vermikulaarisesta raudasta harmaaksi rautaksi tarvitsee vain vähentää aktiivista magnesiumia 0.001%, magnesiumin palaminen ei saa koko osaa muuttumaan hiutalegrafiitiksi. Kun aktiivinen magnesium ei riitä, grafiitti muodostaa ensin hiutaleita ja laajenee ulospäin jähmettyessään, ja magnesium taipuu ja keskittyy kiinteän nesteen rajapinnan etupäähän. Jos aktiivisen magnesiumin alkuperäinen määrä on sopiva, eutektisen rajalle muodostuu vermikulaarinen grafiitti, kuten kuviossa 3 esitetään. Toisin kuin kaikki tavalliset hiutalegrafiitit, näitä eristettyjä hiutalegrafiittitahroja on vaikea havaita ultraäänellä. Todennäköisyys, että ne skannataan ultraäänellä, ei ole suuri.
Magnesiumin herkkyys vermikulaariselle raudalle voidaan osoittaa kuviossa 4: Lisää tonnia kuumaa metallikauhaa vain 10 grammaa magnesiumia. Φ25 -testinäytteeseen dispergoituneet hiutalegrafiittipisteet voidaan muuttaa täysin vermikulaariseksi grafiitiksi. Testaustangon vetolujuus, jossa on hiutalegrafiittitahroja, on vain 300 MPa, kun taas saman testitangon vetolujuus täydellä virratessa saavuttaa 450 MPa.
Inokulantti on myös erittäin herkkä vermikulaarisen raudan vakaalle alustalle, kuten kuvassa 5 esitetään: 80 gramman inokulantin lisääminen yhteen tonniin sulaa rautaa lisää sferoidoitumisnopeutta Φ25 -testipalkissa 3%: sta 21%: iin. Inokulaatiomäärä on suuri ja kideydintä on monia, mikä edistää pallomaisen grafiitin muodostumista. Tämä nostaa vermikulaarisen rautatason korkean pallomaisuuden nopeuteen. Alhainen rokotusnopeus saa alustan liikkumaan alaspäin. Lukuisat tekijät, kuten sulan raudan ylikuumenemislämpötila, pitoaika, raaka -aineiden kemiallinen koostumus, ymppätyyppi ja rokotusmäärä, vaikuttavat vermikulaarisen rautatason sijaintiin.
Kaikkien prosessinhallintatekniikoiden perusvaatimus on mitata ja analysoida tarkasti sulan raudan tila. Vermikulaarisen raudan luotettava tuotannonohjaus edellyttää samanaikaista aktiivisen magnesiumin kriittisen pisteen mittaamista ryömintä-tuhkasiirtymästä, myöhemmän magnesiumpolton asteesta ja rokotusasteesta.
Lämpöanalyysinäyte, 200 grammaa, saadaan lisäämällä Xinte -koetin sulaan rautaan pallostuksen ja inokulaation jälkeen. Kolmen sekunnin lisäysprosessin aikana anturin seinämä ja sula rauta saavuttavat lämpötilan tasapainotilan. Tämä ohutseinäinen näytteenotin, joka poikkeaa tavanomaisesta lämpöanalyysinäytteen kupista, takaa paitsi saman näytteen tilavuuden joka kerta, myös välttää hapettumisen sulan raudan kaatamisessa näytekuppiin. Ylikuumenemismittaus on tarkempi, koska tavanomaisessa lämpöanalyysissä ei ole sellaista ilmiötä kuin voimakas kondensoituminen.
Kuten kuviossa 6a esitetään, Xinte -anturi on valmistettu puristetusta venytetystä teräslevystä. Se on pohjimmiltaan pallomainen säiliö. Ohut terässeinä, joka sisältää sulan rautaa, sisältää tyhjöpullomaisen eristekerroksen. Eristekerroksen paksuus on sakeutettu symmetrisesti korkeussuunnan mukaisesti tasaisen lämmönpoiston ja jäähdytyksen varmistamiseksi ympäristöön, ja siinä oleva rautainen zz -vesi on lähellä pallomaisen rungon jähmettymistä. Anturin suojaputkessa on kaksi N-tyypin termoparia. Termoelementti voidaan vetää ulos jokaisen mittauksen jälkeen ja käyttää toistuvasti yli 100 kertaa. Toinen kahdesta termoparista sijaitsee säiliön pohjassa ja toinen säiliön lämpökeskuksessa. Koska säiliö on pallomainen ja vapaasti ripustettu (tämä eroaa tavanomaisesta lämpöä analysoivasta näytekupista, joka lepää lämpöä absorboivalla kiinnikkeellä), sula rauta tuottaa tasaisen lämpövirran säiliössä, kuten kuviossa 6b esitetään. Tämä lämpövirta aiheuttaa sulan raudan jatkuvan vaihdon säiliössä muodostaen virtausosuuden mittapään pohjalle.
Jotta voidaan jäljitellä sulan raudan luonnollista häviämistä kaatamisen aikana, anturin seinällä on pinnoite, joka reagoi aktiivisen magnesiumin kanssa. Sula rauta virtaa päällystettyä seinää pitkin lämpövirran ohjaamana. Reaktion jälkeen sulan raudan magnesiumpitoisuus laskee ja kerääntyy astian pohjassa olevaan osastoon. Suoraan sanottuna: Anturin keskellä oleva termopari mittaa reagoimatonta sulaa rautaa, joka on kaatamisen alkutila; pohjassa oleva termopari mittaa tilan kaatamisen jälkeen. Reaktiivisen pinnoitteen koostumus on hyvin erityinen. On varmistettava tarkasti, että osastoon kertynyt sula rauta on 0.003% vähemmän aktiivinen kuin keskisula. Siksi, jos alkuperäinen magnesiumpitoisuus on liian lähellä hiipivän tuhkan käännekohtaa, lokerossa oleva sula rauta tuottaa harmaata rautaa, joka mitataan tämän alueen lämpöparilla. Tällä tavalla työpaja voi valun alussa lisätä magnesiumia väistämättömän magnesiumpolttohäviön kompensoimiseksi.
Jos pohjassa oleva termoelementti näyttää vermikulaarisen rautakäyrän, se osoittaa, että alkuperäinen magnesiumpitoisuus on riittävän korkea, jotta grafiittihiutaleita ei tule valun päätyttyä.
Kuva 7 on Xinte-koettimen poikkileikkauseroosiokaavio näytteen mittauksen jälkeen. Kuvassa näet selvästi osioalueen, päänäytealueen ja termoparin suojaputken. Kun aktiivinen magnesium vähenee 0.003%, erotusvyöhykkeeseen muodostuu D-muotoinen grafiitti- ja ferriittimatriisi. Pohjassa olevan hiutalegrafiittialueen koko kuvastaa suoraan päänäytealueen alkuperäistä magnesiumpitoisuutta. Tämän vyöhykkeen koko voidaan laskea pohjassa vapautuvasta lämmöstä. Varianssi regressiokerroin lämmön vapautumisen ja osion koon välillä ylittää 0.9, mikä osoittaa, että näiden kahden välinen suhde on hyvin tiivis. Vapautettu lämpö saadaan jäähdytyskäyrän aikaintegraatiosta. Tämä menetelmä sulan raudan tilan mittaamiseksi virralla ja kaatamisen lopussa samanaikaisesti takaa magnesiumpitoisuuden tarkkuuden ennen kaatamista.
Koska vermikulaarinen rauta on erittäin herkkä pallomaisille aineille ja ymppäysaineille, valimoiden on mahdotonta käyttää harmaan ja pallografiittivaluraudan valmistuksessa käytettyjä liiallisia käsittelymenetelmiä. Kuten kuvassa 8 esitetään, vermikulaarinen rauta on herkkyytensä vuoksi vakaa vain neliöikkunassa, ei vain magnesiumalustan alueella. Luotettavan vermikulaarisen raudan tuotantoprosessin on hallittava pallomaisuutta ja inokulaatiota alusta loppuun sen varmistamiseksi, että metallografinen rakenne täyttää tavoitteen.
Riippumatta siitä, kuinka paljon työtä tehdään, riippumatta siitä, kuinka tiukka hallinto on, sulan raudan vaihtelu on aina väistämätöntä. Puhumattakaan siitä, kuinka tarkat ihmiset tietävät sulan raudan käsittelystä, yksivaiheiset käsittelymenetelmät, kuten voileipämenetelmä, eivät voi taata, että jokainen käsittely kuuluu kapean vermikulaarisen rautaikkunan sisään. Lukuisia tuotantomuuttujia, kuten sekoitussuhde, uunin lämpötila, pitoaika, sulan raudan kauhan esilämmitysaste, kierteitysnopeus, sulan raudan koputusasento (sisä- tai ulkopuolinen mittaus), sulan raudan paino, seosteräpussin kunto, pallomainen aine todellinen magnesiumpitoisuus (PeSiMg), kunkin kerroksen seosjärjestely kerrosmenetelmässä ja rautaromun peittojen peitto jne. vaikuttavat kaikki magnesiumin imeytymiseen. Näiden tekijöiden lisäksi aktiivisen hapen ja aktiivisen rikin pitoisuus muuttaa myös vermikulaarisen rautaikkunan kokoa ja sijaintia. Muutokset sulan raudan viipymisajassa kauhassa, kuljetusaika ja kaatoaika muuttavat käytettävissä olevaa palamisaikaa.
Eniten arvaamattomia vaihtelutekijöitä ovat kuitenkin käyttäjän virheet tai eri toimijoiden väliset erot, jotka johtuvat erilaisista työtapoista.
Suuressa massatuotannossa ainoa turvallinen tapa on mitata sulan raudan jähmettymisominaisuudet käsittelyn jälkeen. Tällä tavoin erilaiset vermikulaarisen rautaikkunan kokoon, asentoon ja seoksen imeytymiseen vaikuttavat tekijät on mitattu, analysoitu ja harkittu kattavasti. Sitten voidaan lisätä sopiva määrä magnesiumia ja ymppäysainetta. Jokainen kauha sulaa rautaa kaadetaan sen jälkeen, kun se on päivitetty ihanteelliseen tilaan. Tämä kaksivaiheinen mittaus- ja säätöprosessin ohjausmenetelmä minimoi tuotannon vaihtelun ja eliminoi kokonaan vaahdon hiutalegrafiitin riskin.
Vermikulaarisen raudan tuotannon prosessinhallinta kuumalla metallikauhalla
Kuten kuviossa 9 esitetään, prosessin ohjaus alkaa sulan raudan lämpöanalyysillä ensimmäisen pallomaisen ja inokulaatiokäsittelyn jälkeen. Analyysituloksen mukaan langansyöttölaite näyttää automaattisesti langan pituuden, joka lisätään magnesiumilla ja inokulantilla, ja odottaa, että käyttäjä aloittaa sen. Kun syöttölinja on valmis, kauha lähetetään heti valulinjalle. Koko mittaus- ja säätöprosessi kestää noin kolme minuuttia. Tänä aikana työpaja voi suorittaa tavanomaisia esivaluhoitoja, kuten kuonan poistoa. Tämä varmistaa valulinjan jatkuvuuden.
Toiminnallisesta näkökulmasta raaka sula rauta ei sisällä magnesiumia, ja sen hautomiskyky on myös hyvin rajallinen. Sferoidoitumisen ja ymppäyksen jälkeen magnesium ja ymppäysaineet syövät ensin sulassa raudassa olevaa aktiivista happea ja rikkiä ja "hyppäävät" sitten rautaa tiettyyn kohtaan laudalla. Kuvion 10 esimerkissä sulan raudan magnesiumindeksi ja ymppäysindeksi ovat vastaavasti 65. Koska varjotuotannon tärkeimmät muutosparametrit näkyvät sulassa raudassa mittauksen ja käsittelyn jälkeen, termisen analyysin tulokset heijastavat suoraan sulan raudan nykyistä tilaa. Jäljellä on vain lisätä sopiva määrä magnesiumia ja ymppäysainetta sulan raudan nostamiseksi sen hetkisestä paikasta vaadittuun lähtökohtaan. Kuvan 45 esimerkissä lisätään ensin seitsemän yksikköä magnesiumkaapelia ja sitten 10 yksikköä ymppäyskaapeleita. Vastaava suhde indeksiyksikön ja kaapelin pituuden välillä kalibroidaan tuotteen ja korjaamon mukaan ja kootaan ohjelmaan. Lähes 23 100,000 vermikulaarisen valukappaleen aiemman kokemuksen perusteella lisätyn magnesiumkaapelin keskimääräinen määrä on 5 metriä tonnia kohden. Se sisältää 12 grammaa magnesiumia metriä kohti, ja 50%: n imeytymisnopeudella laskettuna magnesiumin määrä sulaa rautaa kohti on vain 30 grammaa. Koska lisäysmäärä on hyvin pieni ja tärkeimmät muutokset ovat jo tapahtuneet alkukäsittelyssä, säätö on erittäin tehokas ja luotettava. Säädön jälkeen lämpöanalyysiä ei tarvitse tehdä.
Ensimmäisessä käsittelyssä käsittelyn jälkeisen tilan tulisi olla alempi kuin kaatopaikka, niin että vaikka kaikki magnesiumin ja ymppäysnesteen imeytymistä edistävät tekijät saavuttavat optimaalisen arvon, sula rauta saavuttaa vain alkuvaiheen . Lukuun ottamatta liiallista käsittelyä, sula rauta ei käsittelyn jälkeen ole harmaan ja valkoisen raudan tilassa. Valuprosessin tehostamiseksi kunkin sulan raudan kauhan magnesiumindeksi ja rokotusindeksi näytetään prosessilohkokaaviossa. Lohkokaavion muuttuvan trendin mukaan käyttäjä voi säätää seuraavaan kauhaan lisätyn sulan raudan määrää. Hiiliekvivalenttiarvo näkyy myös näytöllä. Näitä tietoja on muokattu ja tallennettu tuotantolokiin, jotta ne ovat jäljitettävissä ja kattavia, ja ne täyttävät myös laadunvarmistuksen vaatimukset.
Vaikka lämpöanalyysi ja myöhemmät säädöt voivat varmistaa vermikulaarisen raudan tuotannon, on suositeltavaa ottaa näytteitä lopullisen valun spruekupista analysointia varten. Perinteiseen laatutarkastukseen verrattuna tämä lämpöanalyysitulos voi tarjota online -analyysin ja luokitella valut tarvittaessa. Magnesiumhäviön simulointi anturissa tekee tästä "tuhoamattomasta" tarkastustekniikasta tehokkaamman kuin metallografiset ja ultraäänimenetelmät. Koska tämä menetelmä mittaa suuremman näytteen koon, se havaitsee myös sen, kuinka sula rauta kiinteytyy seuraavan 10-15 minuutin aikana.
Yhteenvetona
Prosessin ohjausjärjestelmän valinta riippuu tuotteesta ja valuprosessista. Valettaessa monimutkaisia tuotteita, kuten vermikulaarista rautamoottorin kantta ja sylinteriä, järjestelmän on samanaikaisesti ohjattava magnesiumin ja ymppäysnesteen pitoisuutta niin, että se on hyvin kapeassa ikkunassa kaatamisen alusta loppuun. Sferoidoitumisnopeuden on oltava 0–20% (hiipumisaste 80–100%) parhaan valettavuuden, mekaanisen lisäyksen ja muun kattavan suorituskyvyn sekä parhaan käyttötoiminnon varmistamiseksi. Hiutalegrafiittitahrat on poistettava kokonaan paikallisten vikojen ja heikkouksien estämiseksi.
Minkä tahansa prosessinohjausjärjestelmän lähtökohta on mitata tarkasti ja tehokkaasti sulan raudan tila. Luotettavassa laajamittaisessa vermikulaarisessa raudantuotannossa on oltava toteutettavissa olevat valvontamenetelmät prosessimuutosten ja ihmisen toimintavirheiden poistamiseksi. Tehokkain tapa eliminoida prosessimuutokset on suorittaa lämpöanalyysi sulasta raudasta pallomaisuuden ja ymppäyksen jälkeen. Lämpöanalyysitulosten mukaan lisätään tarkka määrä magnesiumia ja inokulanttia ennen kaatamista. Tämä online-mittaus- ja säätömenetelmä varmistaa valutuotantolinjan vakauden ja eliminoi erilaiset riskit, jotka aiheutuvat suuren vermikulaarisen raudan tuotannosta.
Säilytä tämän artikkelin lähde ja osoite uudelleenpainamista varten: Vermikulaarisen raudan tuotannon prosessinohjaus
Minghe Die Casting Company ovat omistautuneet valmistukseen ja tarjoavat laadukkaita ja korkean suorituskyvyn valukomponentteja (metalliset painevalukappaleet sisältävät pääasiassa Ohutseinäinen valukappale,Kuuma kamari die casting,Kylmäkammion die casting), Pyöreä palvelu (painevalupalvelu,CNC-työstö,Muotin valmistus, Pintakäsittely) .Jokainen räätälöity alumiinipainevalu, magnesium- tai Zamak / sinkkipainevalu ja muut valutarvikkeet ovat tervetulleita ottamaan yhteyttä meihin.
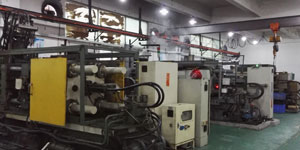
Kaikki prosessit suoritetaan ISO9001: n ja TS 16949: n valvonnassa satojen kehittyneiden painevalukoneiden, 5-akselisten koneiden ja muiden laitteiden kautta, aina blastereista Ultra Sonic -pesukoneisiin. kokeneiden insinöörien, käyttäjien ja tarkastajien tiimi asiakkaan suunnittelun toteuttamiseksi.
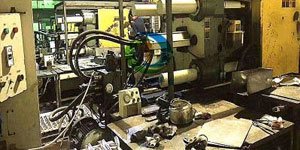
Painevalujen sopimusvalmistaja. Toiminnot sisältävät kylmäkammion alumiinipainevalukappaleet, joiden paino on 0.15 paunaa. 6 lbs., nopea vaihto ja koneistus. Lisäarvopalveluihin kuuluvat kiillotus, tärinä, purseiden poisto, puhallus, maalaus, pinnoitus, päällystys, kokoonpano ja työkalut. Materiaalit, joiden kanssa on työskennelty, sisältävät seoksia, kuten 360, 380, 383 ja 413.
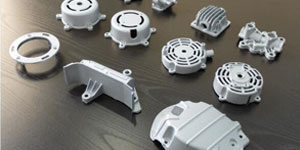
Sinkkipainevalusuunnitteluapu / samanaikaiset suunnittelupalvelut. Mukautettujen sinkkipainevalujen valmistaja. Pienikokoisia valuja, korkeapainevalukappaleita, moniliukuisia muottivaluja, tavanomaisia muottivaluja, yksikkömuotteja ja itsenäisiä muottivaluja ja ontelosuljettuja valukappaleita voidaan valmistaa. Valukappaleita voidaan valmistaa pituudeltaan ja leveydeltään jopa 24 tuumaa +/- 0.0005 tuuman toleranssilla.
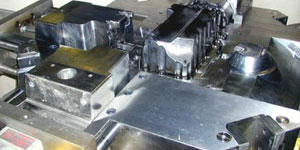
ISO 9001: 2015 -sertifioitu painevaletun magnesiumin valmistaja, ominaisuuksia ovat korkeapaineinen magneettivalumuotoinen valu jopa 200 tonnin kuumakammioon ja 3000 tonnin kylmäkammioon, työkalujen suunnittelu, kiillotus, muovaus, työstö, jauhe- ja nestemaalaus, täydellinen laadunvalvonta CMM-ominaisuuksilla , kokoonpano, pakkaus ja toimitus.
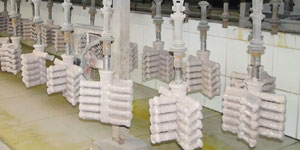
ITAF16949-sertifioitu. Lisävalupalvelu sisältää investointien valu,hiekkavalu,Painovoima valu, Lost vaahto valu,Keskipakovalu,Tyhjö valu,Pysyvä muottien valuKykyihin kuuluvat EDI, tekninen apu, vankka mallinnus ja toissijainen käsittely.
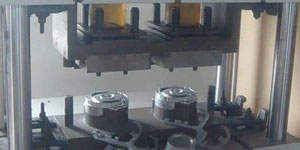
Casting Industries Osatapaustutkimukset: Autot, polkupyörät, lentokoneet, soittimet, vesijetit, optiset laitteet, anturit, mallit, elektroniset laitteet, kotelot, kellot, koneet, moottorit, huonekalut, korut, jigit, tietoliikenne, valaistus, lääkinnälliset laitteet, valokuvauslaitteet, Robotit, veistokset, äänilaitteet, urheiluvälineet, työkalut, lelut ja paljon muuta.
Mitä voimme auttaa sinua tekemään seuraavaksi?
∇ Siirry kotisivulle Die Casting Kiina
→Valuosat- Selvitä, mitä olemme tehneet.
→ Ralated-vinkkejä Die Casting palvelut
By Minghe-painevaluvalmistaja | Luokat: Hyödyllisiä artikkeleita |Materiaali Tunnisteet: Alumiinin valu, Sinkkivalu, Magnesiumvalu, Titaanivalu, Ruostumattoman teräksen valu, Messinkivalu,Pronssivalu,Suoratoista video,Yrityksen historia,Alumiinivalu | Kommentit pois päältä