Kyllästystekniikan soveltaminen moottorinvalmistuksessa
Kevyistä materiaaleista, kuten alumiinisylintereistä, valmistettujen osien kyllästäminen voi tehokkaasti vähentää työkappaleiden romutusastetta ja parantaa niiden laatua merkittävästi. Tuotteiden laadun varmistamisen lähtökohtana ne voivat tehokkaasti alentaa valmistuskustannuksia ja parantaa tuotannon tehokkuutta.
Ehdotus moottorin kevyestä ja kyllästyskäsittelystä
Kevyestä on tullut trendi nykyaikaisessa autoteollisuudessa, mikä johtuu pääasiassa maailmanlaajuisesta huomiosta ympäristönsuojeluun ja energiansäästöön. Tiedot osoittavat, että jos auton omaa painoa pienennetään 10%, sen polttoainetehokkuutta voidaan lisätä 15%. Polttoainetehokkuuden paraneminen tarkoittaa, että auton polttoaineenkulutus ja päästöt vähenevät. Siksi auton painon vähentäminen on tehokkain tapa parantaa auton energiansäästöä ja ympäristönsuojelua. Moottori on auton kriittisin suuri kokoonpano, ja sen painon vähentäminen on ratkaisevan tärkeää auton painon vähentämiseksi.
Tekniseltä kannalta on monia keinoja kevyyden saavuttamiseksi, kuten koko koneen rakenteen optimointi, lisämoduulit ja kevyt, mutta kevyiden materiaalien, kuten muovien, alumiiniseosten ja magnesiumseosten käyttö perinteisten materiaalien korvaamiseksi koska valurauta on virran pienennys. Moottorin painon tärkein tapa. Itse asiassa alumiiniseosta on käytetty laajalti moottorin sylinterinkannessa, imusarjassa ja pienemmissä osissa, kuten vesipumpun koteloissa ja öljypumpun koteloissa jo vuosia, ja yhä useammat yritykset ovat ottaneet käyttöön alumiiniseoksesta valmistettuja sylinterilohkoja viimeisen vuosikymmenen aikana. Valurautaan verrattuna alumiinivalut ovat kuitenkin alttiimpia sisäiselle löystymiselle, kutistumiselle ja huokosille valuprosessin aikana kiteiden muodostumisen, kutistumisen ja kaasun imeytymisen vuoksi. Näissä viallisissa valukappaleissa on tiheä pintakerros koneistuksen jälkeen. Alue poistetaan, mikä paljastaa sisäiset organisatoriset viat. Niiden alumiinivalujen osalta, jotka vaativat tiiviyttä moottorissa, vuotojen havaitsemisprosessin läpi tuotantolinjalla vialliset mikrohuokoset aiheuttavat liiallista vuotoa ja tuottavat jätettä, joskus jopa erissä. Koska nämä olosuhteet voidaan havaita vasta useiden koneistusten jälkeen, ne aiheuttavat myös vakavaa työtuntien, raaka-aineiden ja energian tuhlausta. On nähtävissä, että alumiinivalujen suuren romumäärän ongelman ratkaisemiseksi tuotannossa on toteutettava tiettyjä käsittelytoimenpiteitä. Tällä hetkellä yleisimmin käytetty tekniikka on kyllästyskäsittely eli vuotojen sulkeminen. Niin kutsutun "kyllästyksen" tarkoituksena on tunkeutua tunkeutuva aine alumiinivalun mikrohuokosiin tietyissä olosuhteissa, ja jähmettymisen jälkeen huokosiin ja valun huokosten sisäseinään tunkeutunut täyteaine yhdistetään kokonaisuudessaan tukkia mikrohuokoset niin, että osat täyttävät prosessitekniikan, jota tarvitaan paineistukseen, vuotoon ja vuotoon.
Tyhjiöpaine kyllästysprosessi
Tällä hetkellä alumiinivalujen valmistuksessa kotimaassa ja ulkomailla käytetään yleensä tyhjiöpaineensuodatusmenetelmää. Tämä prosessi suoritetaan pääasiassa tyhjiöpainesäiliössä. Prosessivirran mukaan se voidaan jakaa kolmeen vaiheeseen: esikäsittely, kyllästyskäsittely ja jälkikäsittely. Sen eri vaiheisiin kuuluu pääasiassa: esikäsittelyä kutsutaan myös mikrohuokoiseksi esikäsittelyksi, joka pääasiassa valujen rasvanpoistoa, puhdistusta ja kuivausta seuraavan prosessin valmistelemiseksi; kyllästyskäsittelyn ensimmäinen vaihe on työkappaleen asettaminen koriin ja sitten kori kyllästysastiaan; imuroi kyllästysäiliö kaasun poistamiseksi osien huokosista; kuljettaa tiivistysaineen varastosäiliöstä kyllästyssäiliöön ja upottaa vielä tyhjiössä olevat osat; Imuroi kyllästysäiliö uudestaan tiivisteen kaasun poistamiseksi; vapauta tyhjiö ja paineista kyllästysäiliö paineilmalla, mikä auttaa työntämään tiivistysaineen huokosiin; vapauta paine ja palauta tiivistysaine varastosäiliöön; Jälkikäsittely on pääasiassa osien irrottamista, linkousta, kuivausta ja huuhtelua.
Esikäsittelyn päätarkoitus on poistaa öljytahrat, metallilastu ja pöly osien pinnalta, parantaa kyllästyksen laatua ja estää öljyn ja mekaanisten epäpuhtauksien pääsy kyllästysnesteeseen tunkeutumisen ja tarttuvuus. Yleisesti käytettyjä rasvanpoistomenetelmiä ovat rasvanpoisto liuottimella, lipeänpoisto ja sähkökemiallinen rasvanpoisto. Valukappaleet poistetaan edellä mainitun rasvanpoiston ja puhdistuksen jälkeen, huuhdellaan kuumalla vedellä ja kuivataan sitten 80-90 ℃. Liotusvaikutuksen parantamiseksi ja tyhjöpumpun sisään pääsemisen estämiseksi suuren määrän vettä kuivaus puhdistuksen jälkeen on erittäin tärkeää.
Kyllästyskäsittelyn tarkoituksena on laittaa esikäsitellyt työkappaleet kyllästyssäiliöön tiivistämään ja tyhjentämään, poistamaan säiliössä oleva ilma ja hieno pöly kokonaan sekä valun huokoset ja luomaan paine-eron dynaamiset olosuhteet täyttöä ja imeytymistä varten kyllästysainetta. Sitten säiliön alipaine imee tunkeutujan sisään ja tyhjiö imetään uudelleen. Toisen imuroinnin tarkoituksena on tyhjentää säiliön kyllästysnesteessä oleva kaasu estääkseen kaasua sisältävän kyllästysnesteen tunkeutumisen valun mikrohuokosiin, jotta vältetään huokosten muodostuminen jähmettymisen aikana, jotka vaikuttavat tiivisteeseen. esitys. Lopuksi paineista niin, että täytetty ja valun huokosiin tunkeutunut tunkeutuva aine tunkeutuu edelleen vian kunkin osan syvimpään kohtaan. Kyllästysaine on nestemäinen aine, joka on valmistettu epäorgaanisista tai orgaanisista aineista. Tällä hetkellä yleisimmin käytetty metakrylaatti PC504/66 -tiiviste kovetetaan kuumennettaessa ja tarjoaa näkyvän mikrohuokostäytteen sen pienellä kutistumisella polymeroinnin aikana. Samalla sen alhainen viskositeetti auttaa tiivistysainetta tunkeutumaan nopeasti ja syvälle mikrohuokosiin. Kovettunut tiivistysaine voi toimia normaalisti alueella -50 ~ 200 ℃.
Jälkikäsittely on tiputtaa työkappale, puhdistaa se ja laittaa se kovetusuuniin jähmettymään niin, että valuhuokosiin tunkeutuva aine muuttuu nesteestä kiinteäksi kiinteäksi kalvoksi. Kovetuslämpötila asetetaan yleensä 80 ~ 90 ℃ tai se sijoitetaan huoneenlämpötilaan (yli 25 ℃) 24 tunniksi. Jos valua käytetään yli 300 ° C: ssa, se tulee kovettaa 80 ° C: ssa 2 tuntia ja sitten 110 ° C: ssa 1 tunti.
Sen suhteen, mikä osa tuotantoprosessista on kyllästetty, eri tuotantolaitokset ja erityyppiset työkappaleet ovat hyvin erilaisia. Pieni joukko yrityksiä laatii yhdenmukaiset määräykset kaikille voimansiirto -osille, jotka edellyttävät suurta valmistustarkkuutta ja ilmatiiviyttä: tällaiset osat on kyllästettävä ennen koneistusta, toisin sanoen silloin, kun ne ovat edelleen valutilassa parannuksen saavuttamiseksi. Valun tarkoitus, pidentää työkalun käyttöikää koneistuksen aikana ja varmistaa tuotteen laatu. Useimmat tehtaat käyttävät kuitenkin edelleen erilaisia menetelmiä erityyppisten osien mukaan. Yleisesti ottaen joidenkin avainosien, kuten moottorin alumiinisen sylinterilohkon, on yleensä pakko kyllästää kaikki osat, kun ne ovat valutilassa, ja lähettää ne sitten. OEM. Mitä tulee joidenkin työkappaleiden kyllästämiseen tiettyjen kriteerien mukaisesti tietyn prosessin jälkeen OEM -tuotantolinjalla, se riippuu OEM -valmistajan valmistusprosessista.
Useimmissa osissa niiden ei yleensä tarvitse olla kyllästettyjä, kun ne ovat valukappaleessa. Sen sijaan kyllästysprosessi toteutetaan tietyn tuotantoprosessin jälkeen todellisen tilanteen mukaan. Toisin sanoen, kun osat useiden koneistusprosessien jälkeen varmistetaan, että joidenkin osien vuodon havaitsemisarvo on määritetyn aikavälin sisällä, vain tämä osa hylätystä työkappaleesta kyllästetään. Useimmissa tapauksissa hylättyjen työkappaleiden osuus on hyvin pieni (noin 1% - 2%), mutta kun tämä osuus ylittää tietyn rajan (tilanteesta riippuen), OEM vaatii aihion tehtaan Kaikki valut on kyllästetty .
Jotkut kyllästyskäsittelyä vaativat osat eivät sisälly OEM -valmistajan valmistusprosessiin rakenteellisista syistä. Niiden osien osalta, joiden vuodonilmaisutulokset ovat toleranssin ulkopuolella, riippumatta siitä, kuinka suuri todellinen mittausarvo on, ne romutetaan suoraan. Jos vuotoarvo kuitenkin ylittää jossain määrin työkappaleen osuuden, päämoottoritehdas esittää myös vaatteen kyllästyskäsittelystä kaikille valutyökaluille.
Joten missä on kyllästyskäsittelyn varsinainen toiminta? Riippumattomat ja ammattitaitoiset yritykset harjoittavat yleistä käytäntöä kotimaassa ja ulkomailla. Tämä ei ole vain tehokasta ja helppoa laadun varmistamiseksi, vaan myös kokoonpanotehtaan kustannukset ovat suhteellisen alhaiset. On kuitenkin myös muutamia moottoritehtaita, joilla on suuret erät, nopea tuotantotahti ja korkeat tuotteiden laatuvaatimukset. Ne avaavat suljetun alueen työpajassa, jotta edellä mainitut kyllästyskäsittelyä harjoittavat ammattitehtaat voivat rakentaa suhteellisen yhden, tehokkaan ja Korkeammalla koneistuksella varustetun kyllästyksen tuotantolinja vastaa työpajan osaa. Tietenkin tämän "työosan" käyttöaste on alhaisempi kuin yleisen tuotantolinjan.
Määrittele useita kyllästettyjen työkappaleiden määritelmiä
Kuten me kaikki tiedämme, sylinterilohko on moottorin päärunkona suurin ja raskain osa niistä. Kun valitaan alumiiniseos, sen painonpudotuksella noin puolet on suurin merkitys moottorin keveydelle. Kun otetaan kuitenkin huomioon sylinterilohkon monimutkainen rakenne ja työstöprosessien määrä verrattuna muihin moottorin alumiinivaluihin, myös alumiinisen sylinterilohkon sisäisten vikojen todennäköisyys valu- ja muovausprosessin aikana on suurempi. Siksi yritykset pitävät eniten huolen siitä, kuinka standardoida ja tehokkaasti ottaa käyttöön upotussuodatusprosessi sen laadun varmistamiseksi. Seuraavassa, esimerkkinä alumiinisylinteri, impregnoitavien työkappaleiden määrittely- ja hyväksymisongelma selitetään edelleen edustavan tapauksen avulla. Äskettäin rakennettu alumiinisylinterin työstölinja modernissa automoottoritehtaassa on suorittanut kaikki karkeat työstöprosessit ennen kuin työkappale saapuu välipuhdistusasemaan. Ennen seuraavan laakerikannen asennusta ja sen jälkeisiä viimeistelytoimia asennettiin tiivistyskoe. Alumiinisen sylinterilohkon matalapaineisen öljykanavan, vesikanavan ja korkeapaineöljykanavan vuotojen havaitsemisen lisäksi tämä asema vastaa myös portin asettamista. Mitatun vuotoarvon mukaan on määritettävä, onko tämä alumiinisylinteri kyllästetty.
Työkappaleelle on asetettu kaksi suojarajaa: ensimmäinen on tarkastetun osan vuotovirta, esimerkkinä matalapaineinen öljykanava, vuotoraja on 30 CC/min; Toinen seulontaraja on Tämä tarkastettu osa on tarkoitus määrittää, onko alumiinisylinterissä vuoto, mutta onko mahdollista ja tarpeellista korjata se kyllästyskäsittelyllä. Ottaen esimerkkinä matalapaineisen öljykanavan taulukosta käy ilmi, että se on 500 CC/min. Tästä syystä, kun alumiininen sylinterirunko välipuhdistusprosessin jälkeen tulee tiivistyskoepaikalle kuljetusradan varrella, jos jokin työkappaleen mitattu vuotoarvo on alempi kuin taulukossa annettu vastaava suojaraja, on, Vuodonopeus katsotaan päteväksi ja sitten se virtaa seuraavaan prosessiin. Mutta niin kauan kuin jokin todellisista mitatuista vuotoarvoista ylittää vuodonopeutensa, mutta on pienempi kuin romuraja, ota esimerkkinä taulukon matalapaineinen öljykanava, vaihteluväli on 30 ja 500CC/min. Alumiinista sylinterilohkoa käsitellään työkappaleena, joka on otettava ulos kyllästyskäsittelyä varten, lähetettävä kilparadalla päinvastaiseen suuntaan ja poistettava sitten manuaalisesti ja lähetettävä pois. Mitä tulee hyvin pieneen määrään työkappaleita, joiden mitattu vuotoarvo on saavuttanut tai jopa ylittänyt taulukon romurajan, ne virtaavat ulos kuljetinradan läpi. Edellä mainitun havaitsemis-, seulonta- ja hajautusprosessin suorittaa robotti tiivistyskoeasemalla.
Yhteenvetona voidaan todeta, että alumiinipullojen ja muiden osien kyllästyskäsittelyn jälkeen romun määrä vähenee ja laatu paranee merkittävästi, mutta myös valmistuskustannukset laadun varmistamiseksi ja tuottavuus paranevat tehokkaasti. Siksi nykyaikaisen automoottoriteollisuuden yhä kevyemmän prosessin aikana tieteellinen ja järkevä soluttautumistekniikan käyttö on paras ratkaisu alumiiniseoksen ja muiden kevyiden materiaalivalujen (kuten vikojen, kuten mikrohuokosten) luontaisten ongelmien ratkaisemiseksi.
Säilytä tämän artikkelin lähde ja osoite uudelleenpainamista varten:Kyllästystekniikan soveltaminen moottorinvalmistuksessa
Minghe Die Casting Company ovat omistautuneet valmistukseen ja tarjoavat laadukkaita ja korkean suorituskyvyn valukomponentteja (metalliset painevalukappaleet sisältävät pääasiassa Ohutseinäinen valukappale,Kuuma kamari die casting,Kylmäkammion die casting), Pyöreä palvelu (painevalupalvelu,CNC-työstö,Muotin valmistus, Pintakäsittely) .Jokainen räätälöity alumiinipainevalu, magnesium- tai Zamak / sinkkipainevalu ja muut valutarvikkeet ovat tervetulleita ottamaan yhteyttä meihin.
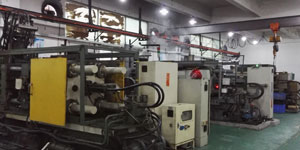
Kaikki prosessit suoritetaan ISO9001: n ja TS 16949: n valvonnassa satojen kehittyneiden painevalukoneiden, 5-akselisten koneiden ja muiden laitteiden kautta, aina blastereista Ultra Sonic -pesukoneisiin. kokeneiden insinöörien, käyttäjien ja tarkastajien tiimi asiakkaan suunnittelun toteuttamiseksi.
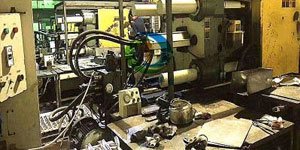
Painevalujen sopimusvalmistaja. Toiminnot sisältävät kylmäkammion alumiinipainevalukappaleet, joiden paino on 0.15 paunaa. 6 lbs., nopea vaihto ja koneistus. Lisäarvopalveluihin kuuluvat kiillotus, tärinä, purseiden poisto, puhallus, maalaus, pinnoitus, päällystys, kokoonpano ja työkalut. Materiaalit, joiden kanssa on työskennelty, sisältävät seoksia, kuten 360, 380, 383 ja 413.
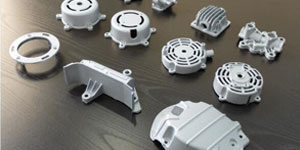
Sinkkipainevalusuunnitteluapu / samanaikaiset suunnittelupalvelut. Mukautettujen sinkkipainevalujen valmistaja. Pienikokoisia valuja, korkeapainevalukappaleita, moniliukuisia muottivaluja, tavanomaisia muottivaluja, yksikkömuotteja ja itsenäisiä muottivaluja ja ontelosuljettuja valukappaleita voidaan valmistaa. Valukappaleita voidaan valmistaa pituudeltaan ja leveydeltään jopa 24 tuumaa +/- 0.0005 tuuman toleranssilla.
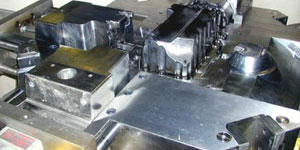
ISO 9001: 2015 -sertifioitu painevaletun magnesiumin valmistaja, ominaisuuksia ovat korkeapaineinen magneettivalumuotoinen valu jopa 200 tonnin kuumakammioon ja 3000 tonnin kylmäkammioon, työkalujen suunnittelu, kiillotus, muovaus, työstö, jauhe- ja nestemaalaus, täydellinen laadunvalvonta CMM-ominaisuuksilla , kokoonpano, pakkaus ja toimitus.
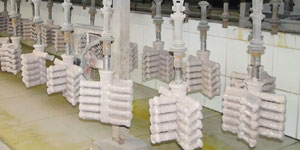
ITAF16949-sertifioitu. Lisävalupalvelu sisältää investointien valu,hiekkavalu,Painovoima valu, Lost vaahto valu,Keskipakovalu,Tyhjö valu,Pysyvä muottien valuKykyihin kuuluvat EDI, tekninen apu, vankka mallinnus ja toissijainen käsittely.
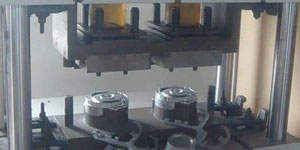
Casting Industries Osatapaustutkimukset: Autot, polkupyörät, lentokoneet, soittimet, vesijetit, optiset laitteet, anturit, mallit, elektroniset laitteet, kotelot, kellot, koneet, moottorit, huonekalut, korut, jigit, tietoliikenne, valaistus, lääkinnälliset laitteet, valokuvauslaitteet, Robotit, veistokset, äänilaitteet, urheiluvälineet, työkalut, lelut ja paljon muuta.
Mitä voimme auttaa sinua tekemään seuraavaksi?
∇ Siirry kotisivulle Die Casting Kiina
→Valuosat- Selvitä, mitä olemme tehneet.
→ Ralated-vinkkejä Die Casting palvelut
By Minghe-painevaluvalmistaja | Luokat: Hyödyllisiä artikkeleita |Materiaali Tunnisteet: Alumiinin valu, Sinkkivalu, Magnesiumvalu, Titaanivalu, Ruostumattoman teräksen valu, Messinkivalu,Pronssivalu,Suoratoista video,Yrityksen historia,Alumiinivalu | Kommentit pois päältä